LED lighting saves 70% of energy compared to the conventional lighting.
We are installing LED lighting at new depots and warehouses, and at existing locations we are replacing regular lighting with LED lighting. LED light saves 70% of energy compared to conventional lighting. Last year this transition was focused on West, Central and Central-East Europe, and the transition will continue in 2021. At LPR, the opening of new service centres is an opportunity to install more environmentally-friendly equipment such as LED lighting and more efficient air compressors. Good examples are the two large depots in the UK that opened last year. Next to LED light and efficient air compressors, electric charging points for cars are also being installed, and the use of daylight is being optimised. In addition, energy efficient equipment from locations that have been closed will be re-used whenever possible.
LED lighting
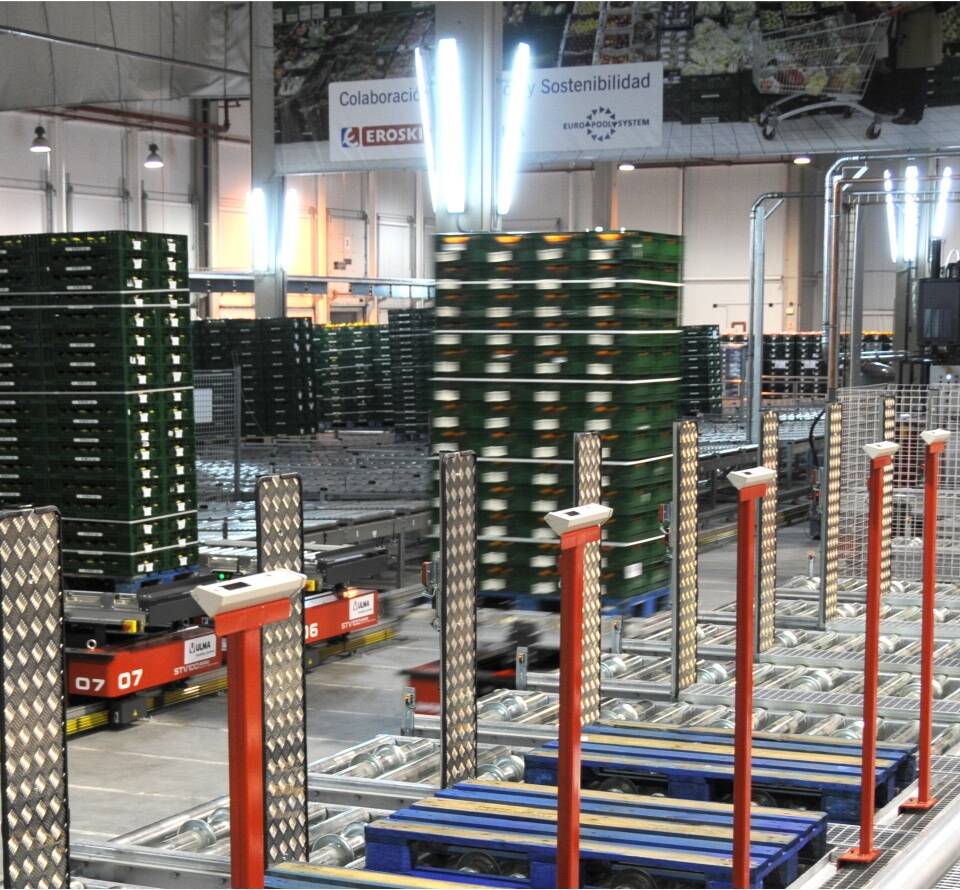

New centrifuges uses 25% less energy compared to the conventional blowers
Together with a partner, we are developing a new type of centrifuge for locations that operate a single line. This centrifuge can be used to dry single trays. The first pilot with the new model starts in 2021. We aim to have replaced all old blowers by energy efficient centrifuges by 2025.
back to top
The EPS depots in Sint-Katelijne-Waver (Belgium), Colruyt (Belgium), Horsens (Denmark), Mutterstadt (Germany) and Obertraubling (Germany) have been equipped with new centrifuges. With this new technology, we save 25% energy in the washing process compared to conventional blowers. These centrifuges are suitable for locations that occupy two or more lines. Annually, this reduces the electricity consumption by about 2,800 MWh.
New detergent leads to energy savings when the washing temperature reduces from 60 to 45 degrees
In response to the tomato virus, EPS introduced a new detergent based on caustic chlorine in 2019. Changing to this detergent has had a direct positive impact on the quality of the washing process. It improves the bacteriological result of the whole washing process. With the new detergent, the washing temperature can be reduced from 60 to 45 degrees Celsius, thus increasing the energy efficiency of the washing process and reducing the carbon footprint. Annually this saves about 4,000 tonnes of CO2 eq.
New detergent
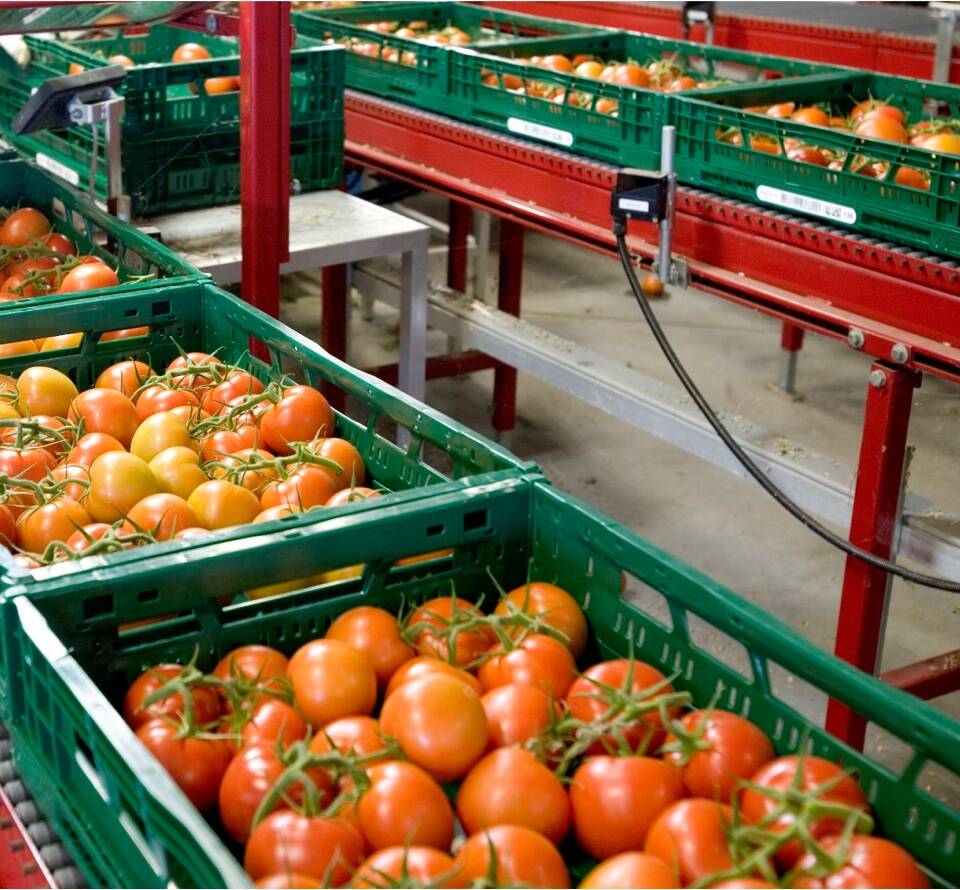
Read more

Saving energy
in our washing process
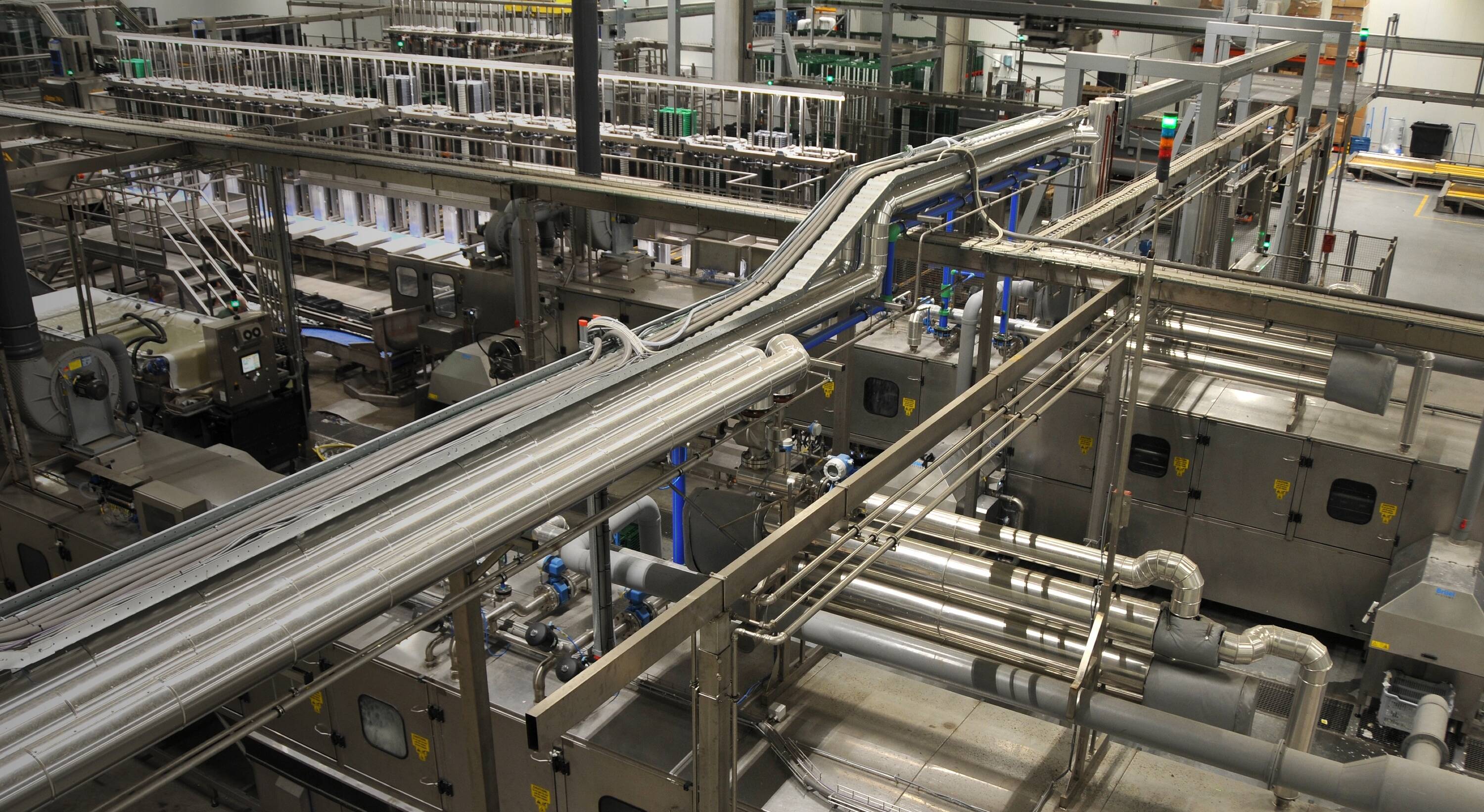
back to top
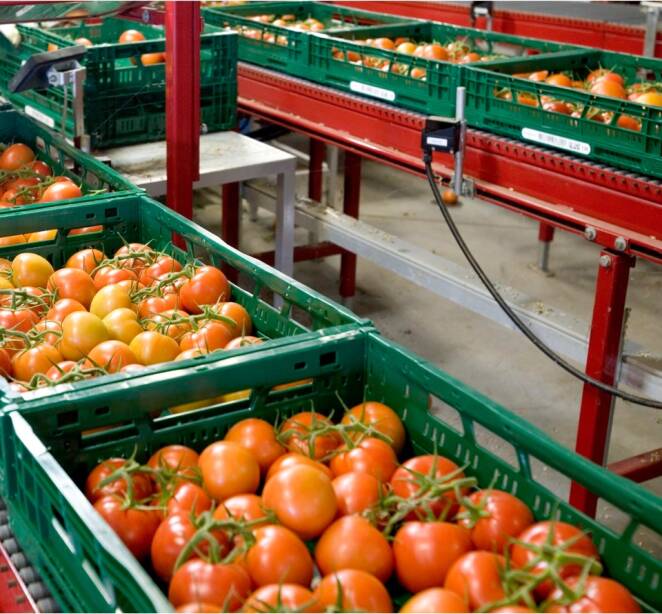
New detergent leads to energy savings when the washing temperature reduces from 60 to 45 degrees
In response to the tomato virus, EPS introduced a new detergent based on caustic chlorine in 2019. Changing to this detergent has had a direct positive impact on the quality of the washing process. It improves the bacteriological result of the whole washing process. With the new detergent, the washing temperature can be reduced from 60 to 45 degrees Celsius, thus increasing the energy efficiency of the washing process and reducing the carbon footprint. Annually this saves about 4,000 tonnes of CO2 eq.
New detergent
LED lighting saves 70% of energy compared to the conventional lighting.
We are installing LED lighting at new depots and warehouses, and at existing locations we are replacing regular lighting with LED lighting. LED light saves 70% of energy compared to conventional lighting. Last year this transition was focused on West, Central and Central-East Europe, and the transition will continue in 2021. At LPR, the opening of new service centres is an opportunity to install more environmentally-friendly equipment such as LED lighting and more efficient air compressors. Good examples are the two large depots in the UK that opened last year. Next to LED light and efficient air compressors, electric charging points for cars are also being installed, and the use of daylight is being optimised. In addition, energy efficient equipment from locations that have been closed will be re-used whenever possible.
LED lighting
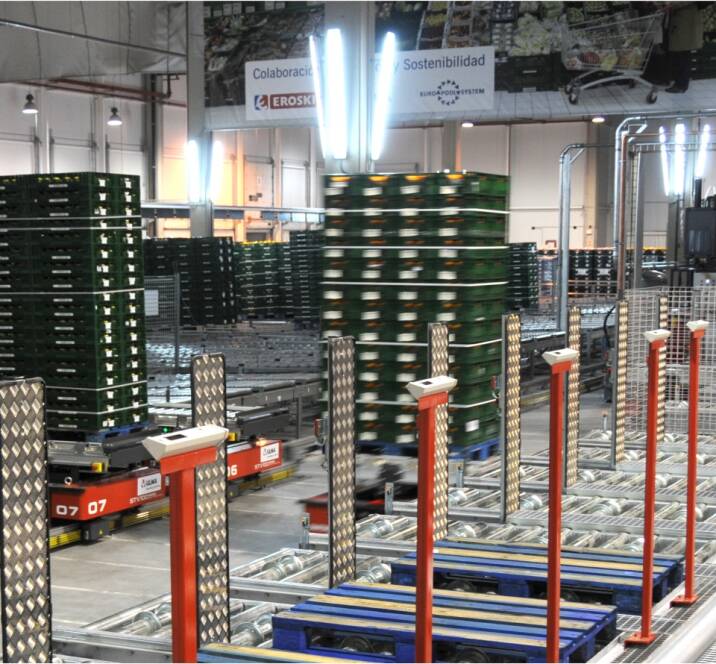
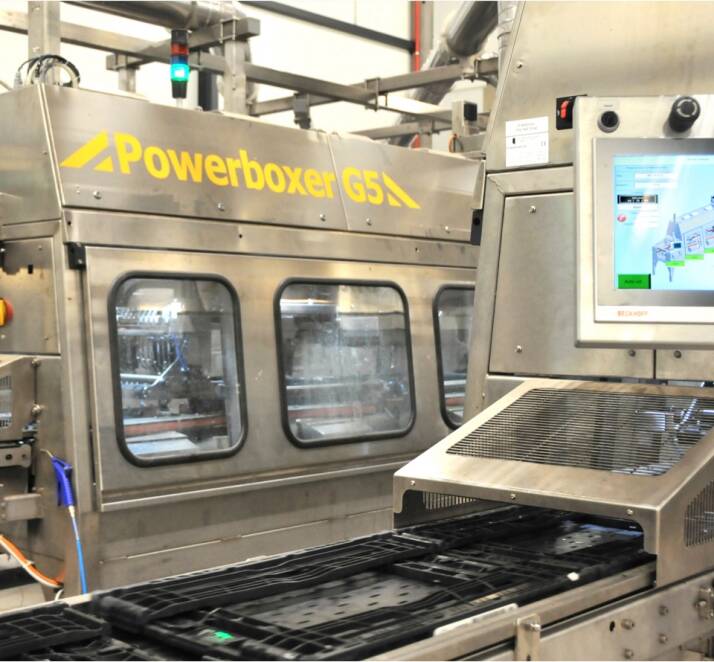
New centrifuges uses 25% less energy compared to the conventional blowers
Together with a partner, we are developing a new type of centrifuge for locations that operate a single line. This centrifuge can be used to dry single trays. The first pilot with the new model starts in 2021. We aim to have replaced all old blowers by energy efficient centrifuges by 2025.
The EPS depots in Sint-Katelijne-Waver (Belgium), Colruyt (Belgium), Horsens (Denmark), Mutterstadt (Germany) and Obertraubling (Germany) have been equipped with new centrifuges. With this new technology, we save 25% energy in the washing process compared to conventional blowers. These centrifuges are suitable for locations that occupy two or more lines. Annually, this reduces the electricity consumption by about 2,800 MWh.
Saving energy in our washing process

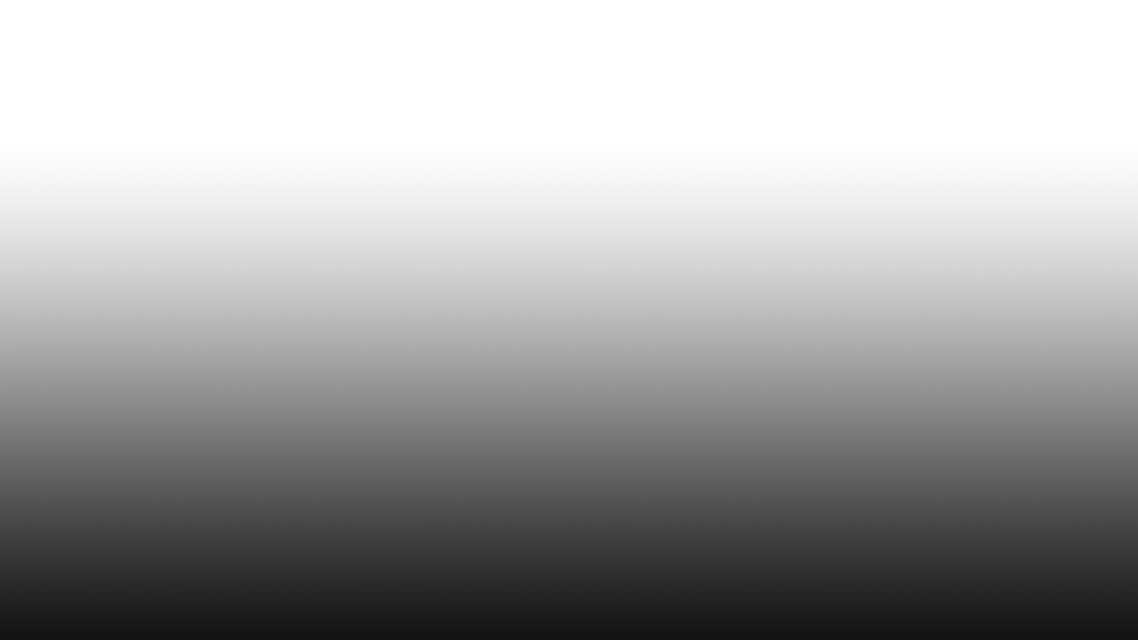
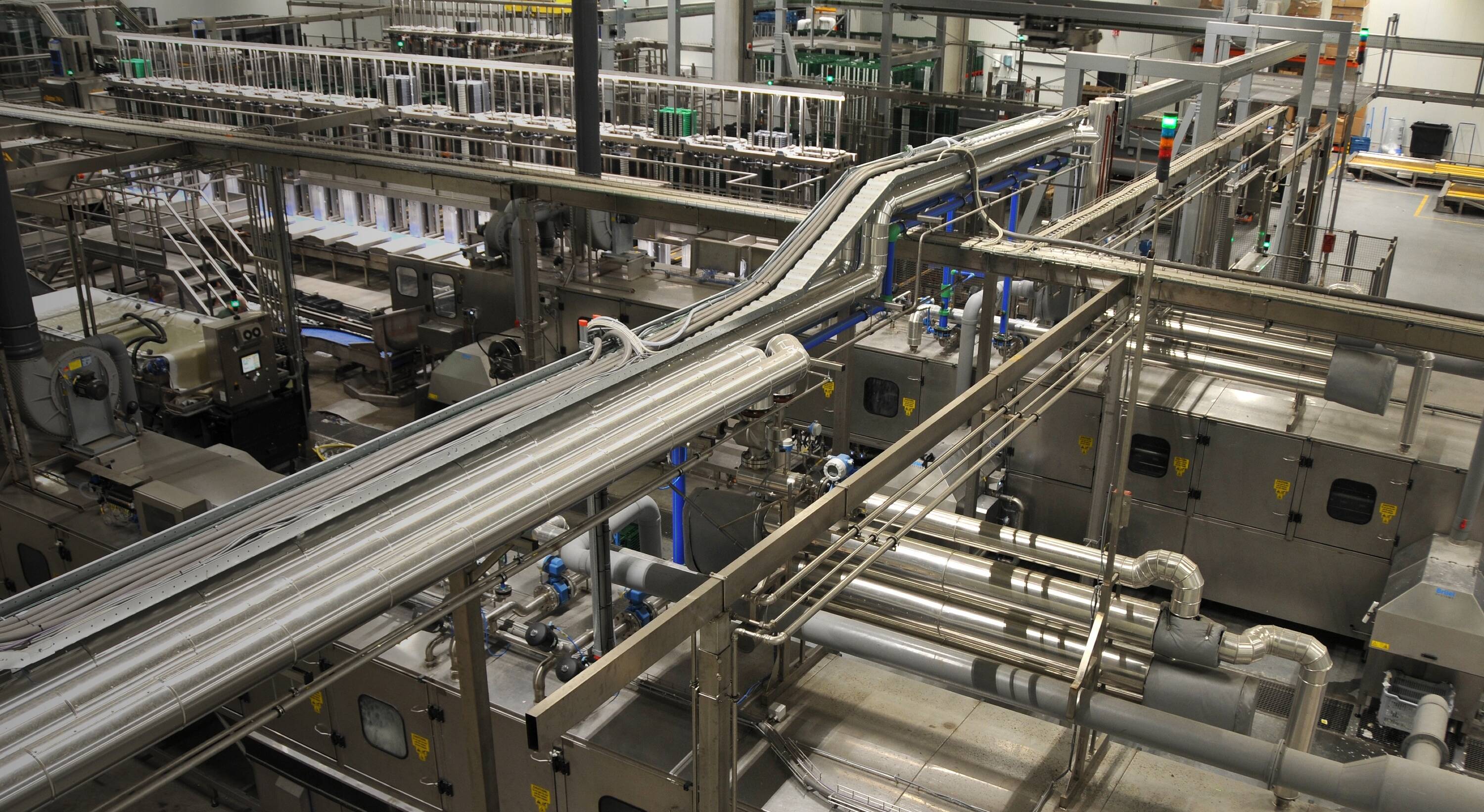