back to top
Summary of goals
and results
Read more
Key facts
and figures
Read more
Saving energy in our washing process
The green energy transition in our depots
Read more
CoolRail:
a new partnership
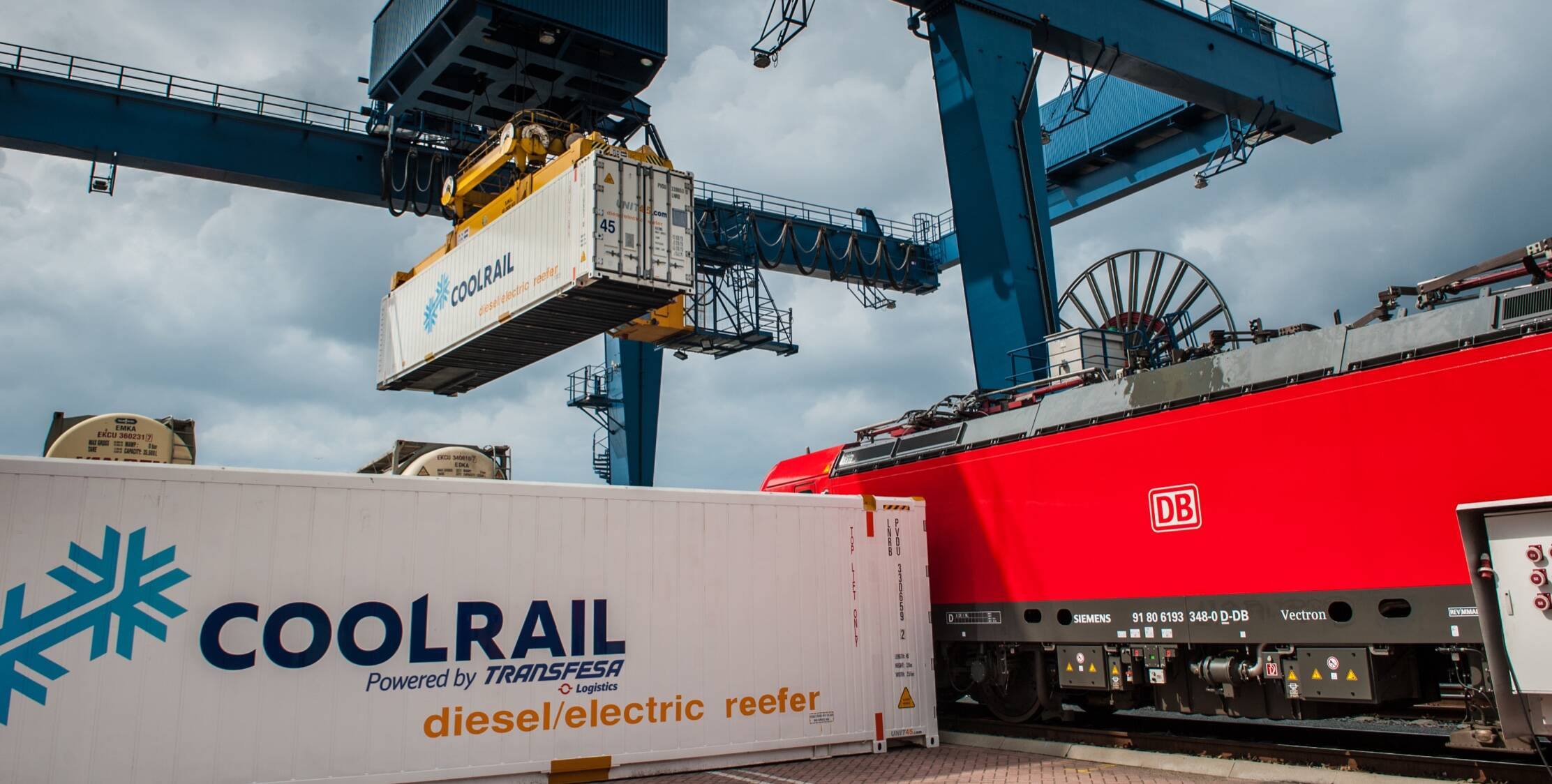
Reducing our carbon footprint
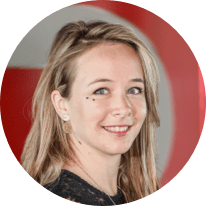
Céline Courrege
”When we are able to anticipate on the future needs of customers, we are able to optimise and improve sustainability”.
Through tooling we can optimise the flows of our pallets across Europe and anticipate any future needs of our customers. This helps us to optimise the transport process. “Having the right pallet at the right place at the right time is extremely relevant for all partners in the supply chain,” Céline explains. “We carefully determine the most optimal flow in terms of transport distance, costs and volumes.”
In addition to optimising the logistic flow, we also use tooling to select the best carriers, based on transport type and transport cost. As this requires less data entry, we gain a great deal of time that we can invest in analysis. Since last summer, LPR has also been using a transport price market tool to gain insight into transport prices and market trends. This is especially helpful to collect management information for new routes.
Tooling is also used to select more sustainable transport modalities. One of the tools gives access to a large database of carriers and actors, including multimodal transport. Sustainability criteria are also used in the selection of carriers. “For example, we can include criteria for trucks with a lower negative environmental impact,” Thibaut says. “The tools allow us to engage with suppliers we did not know before. We need suppliers who can propose alternative ways of working, such as using electric vehicles, so that we can find the right balance between sustainability and profitability.” An example is the short-sea shipping flow between the UK and Spain, and a new route using rail transport between the UK and Italy.
The tools help us to manage change, such as the impact of COVID-19, which has caused soaring customer demand. Besides COVID-19, there has also been the challenge posed by Brexit, especially for LPR. As the UK is no longer an EU country, all pallets entering and leaving the UK now require heat treatment in line with ISPM15 requirements. This has led to various logistic changes in our supply chain. To ensure a smoothly functioning supply chain, we need to include these changes in our optimisation runs. Céline adds, ”By anticipating the future needs of our customers, we can optimise the supply chain and improve its sustainability.” Tooling assists in managing complex situations, in being flexible and in identifying sustainable alternatives. This allows us – together with our partners – to continuously improve sustainability in the supply chain.
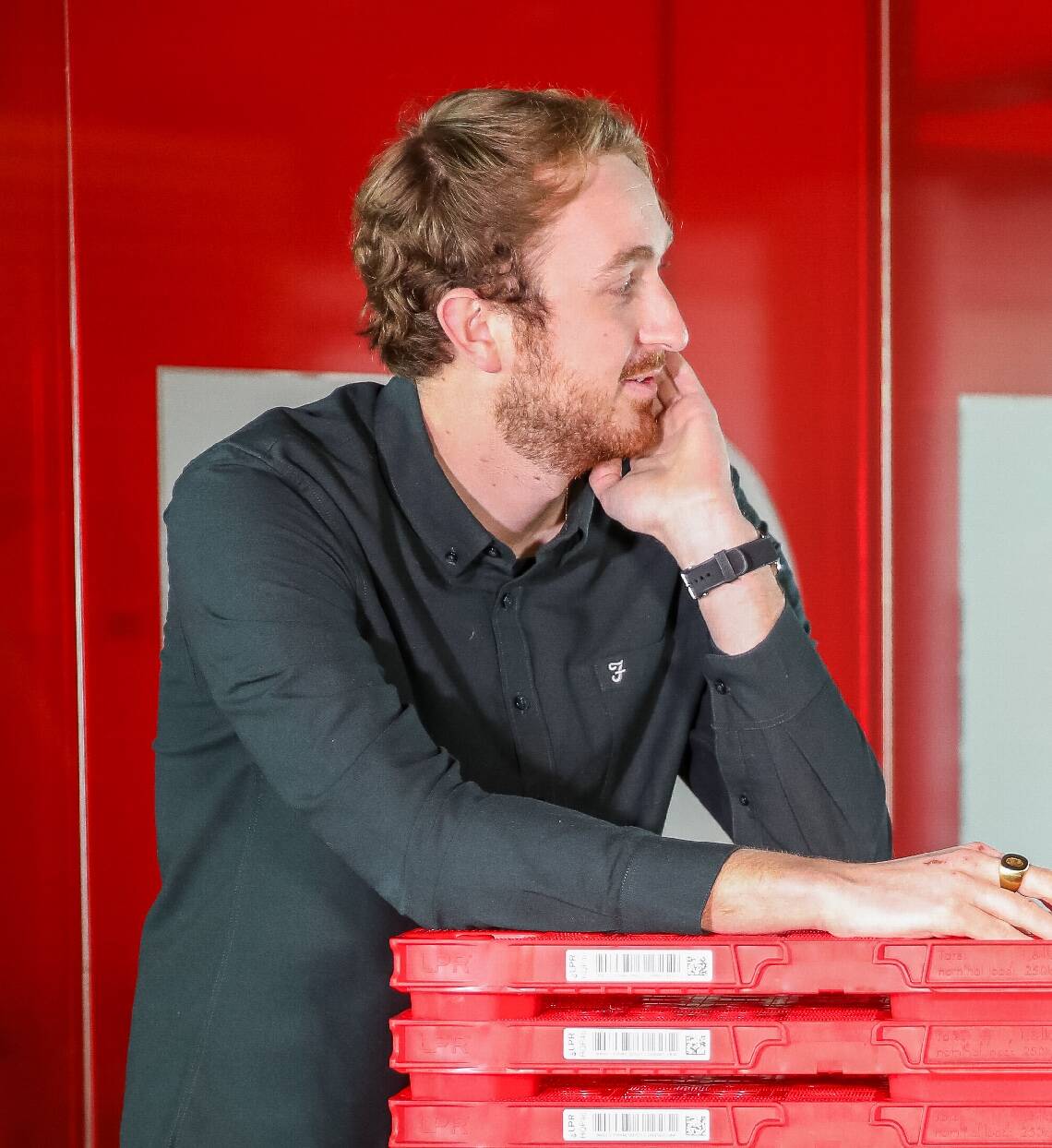
LPR uses innovative tools to optimise transport flows and use more sustainable transport modalities. Transport optimisation allows LPR to take on the role of sustainable catalyst in the supply chain. Two young professionals, Céline Courrege and Thibaut Bernabe, discuss the transport tools they use, and how they support sustainability in the supply chain.
Joint interview with Céline Courrege, Data Analyst Supply Chain at LPR and Thibaut Bernabe, Transport Analyst at LPR
Future-proof transport flows
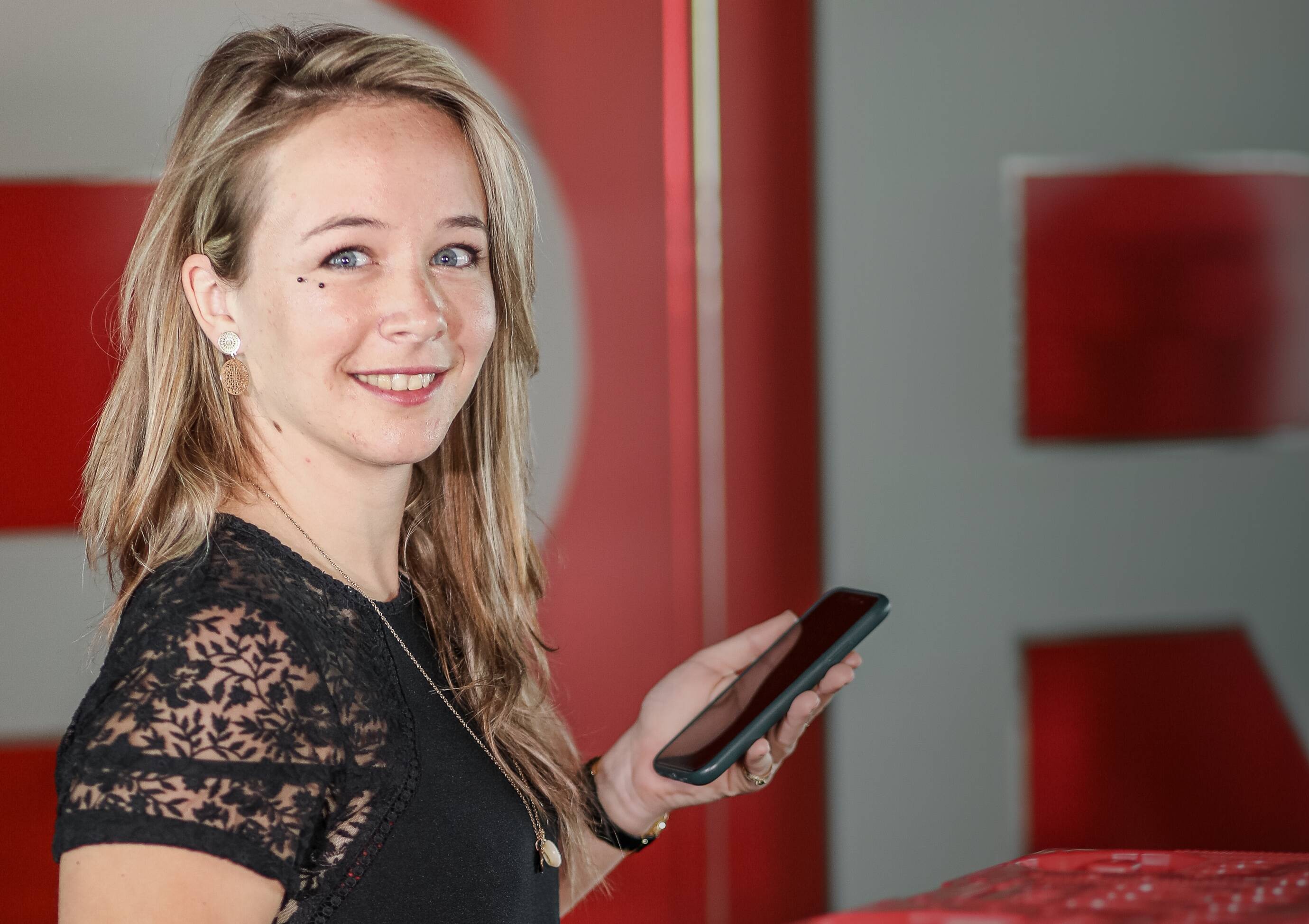

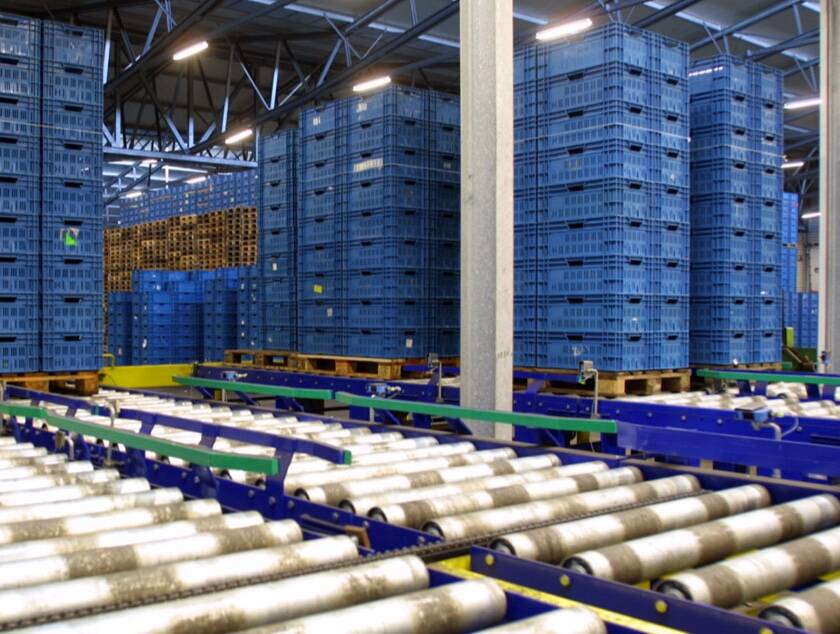
Hans De Bondt
“Switching to green folding trays has an enormous impact on the efficiency of EPS and our partners”
Rigid blue trays are still being used in the Benelux countries. A rigid blue tray occupies seven times more space than a folded green tray. This leads to inefficiencies in the supply chain, which is why the blue trays are being replaced by green folding trays. “As this transition drastically reduces transport movements and need for storage space, it will have an enormous impact on the efficiency of EPS and our partners,” Hans de Bondt explains. Smaller packaging allows for more trays to be transported with one truck. This means that there are fewer trucks on the road and more opportunities to combine transports, thus further reducing our carbon footprint.
Another benefit of the green trays is their full traceability in the supply chain. The trays are equipped with a barcode that is used to track their location. “This allows our customers to return their trays unsorted,” Hans tell us, “and this makes the return process much more efficient for them. The trays rotate faster, and less stock is needed while transport kilometres and costs are being reduced.” To enable the efficient rotation of unsorted returned trays, EPS upgraded the washing and receiving process at its depots. The new installations sort and wash the trays at high speed. The production of the new folding trays was started as early as 2018 in order to ensure enough stock to support the full transition. The old blue trays are now being collected and grinded. The granulate is 100% re-usable, and will be recycled partly for manufacturing new trays and partly as construction material for other purposes.
The first phase of transition started in February 2021. Since then, millions of blue trays have already been replaced. The second phase of the transition is scheduled for September 2021, when the auctions will also switch to green folding trays. EPS expects to recycle about 50 million blue trays in total. Many partners are involved in the project, including retailers, auction houses, logistic service providers and tray suppliers. “The large number of partners involved in the transition was challenging, but we worked together intensively to make the transition happen,” Hans says. “I am proud of the entire EPS team and delighted to see the immediate impact of the project on the sustainability of our supply chain!”
Project Cyan is the transition from rigid blue trays towards a new generation of green folding trays, which started in 2020. The project focuses on the Benelux countries and has an enormous impact on transport movements and CO2 reduction.
Interview with Hans De Bondt, Cyan Project Manager
Project Cyan:
a new generation of green trays
By increasing supply chain efficiency, deploying alternative modes of transport and designing our products optimally, we are reducing our carbon footprint and are contributing to the sustainability ambitions of our customers.
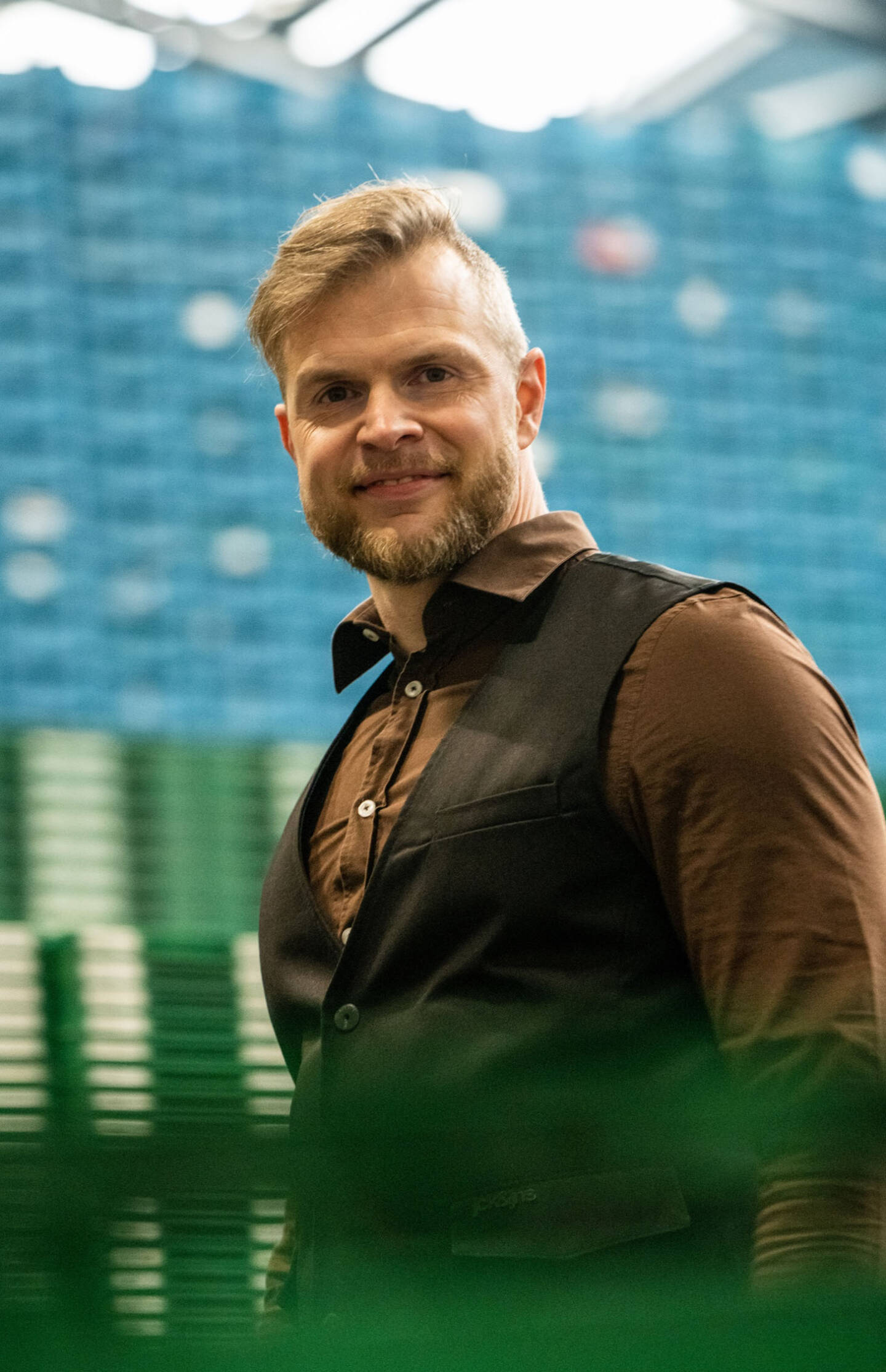
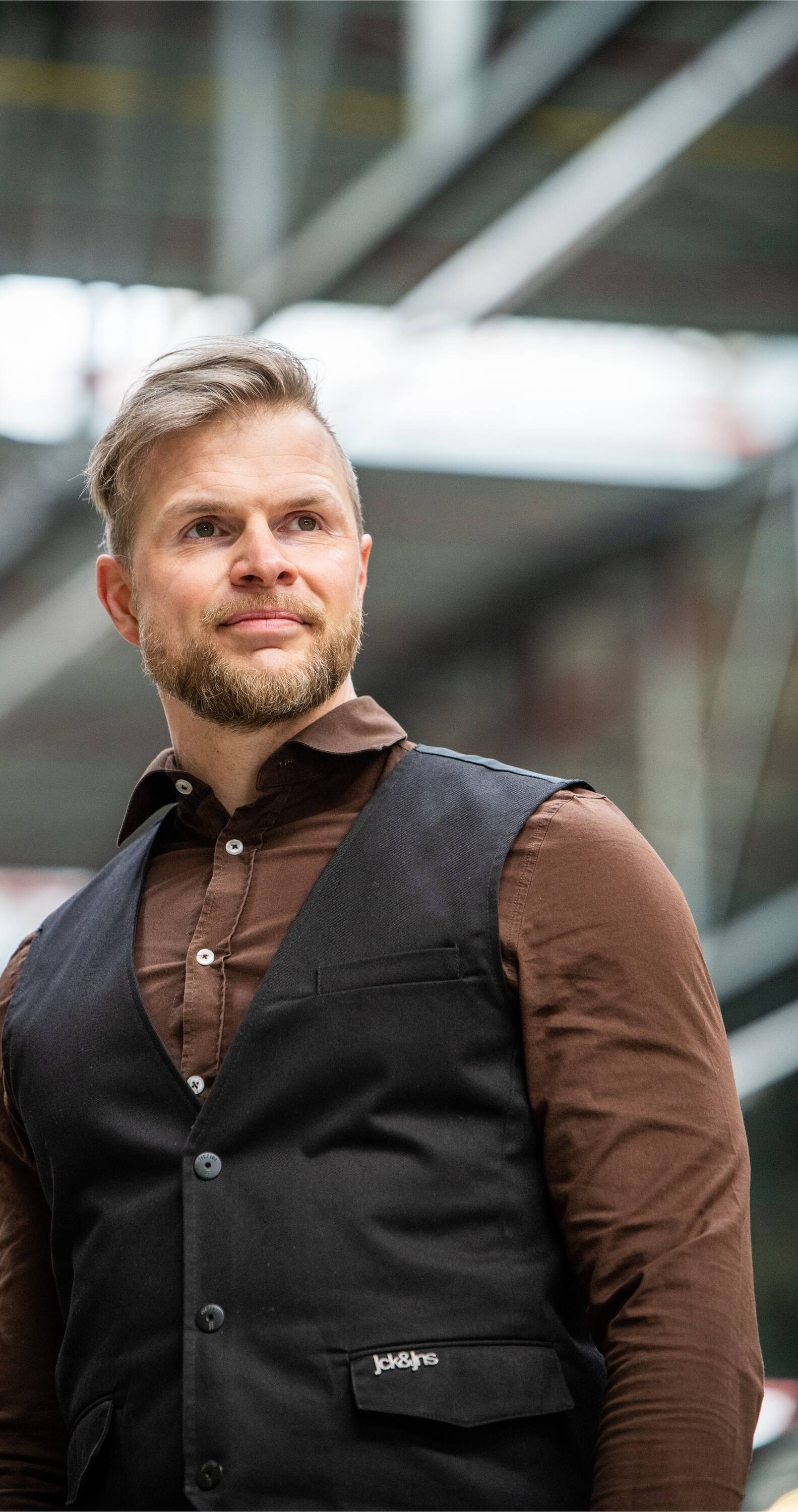
Read more
Planet

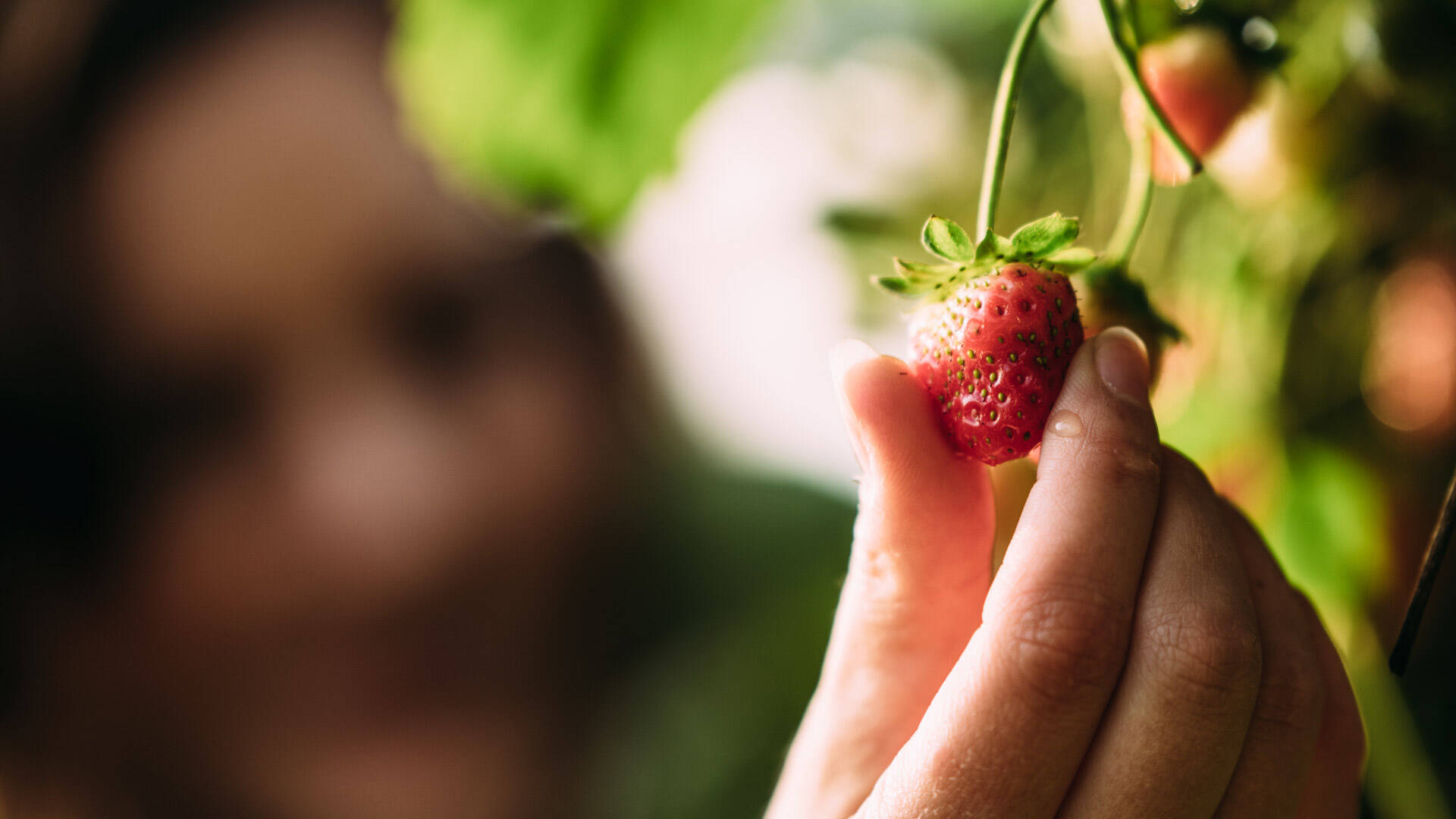
back to top
Summary of goals and results
Key facts
and figures
Read more
Saving energy in our washing process
The green energy transition in our depots
CoolRail:
a new partnership
Read more
Read more
Reforestion: replanting trees
in France
Green
energy
contracts
Read more
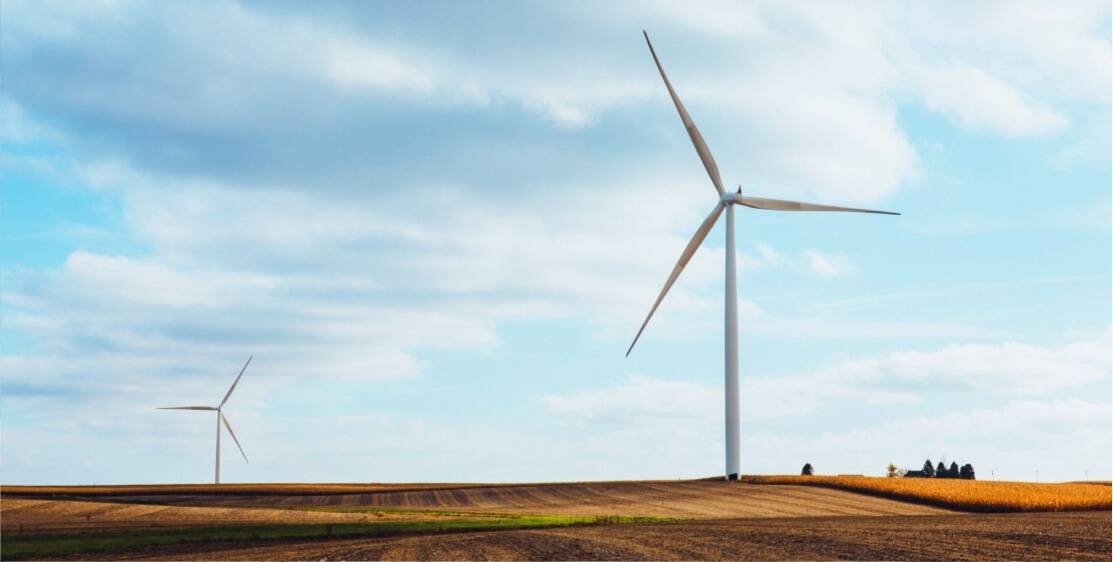
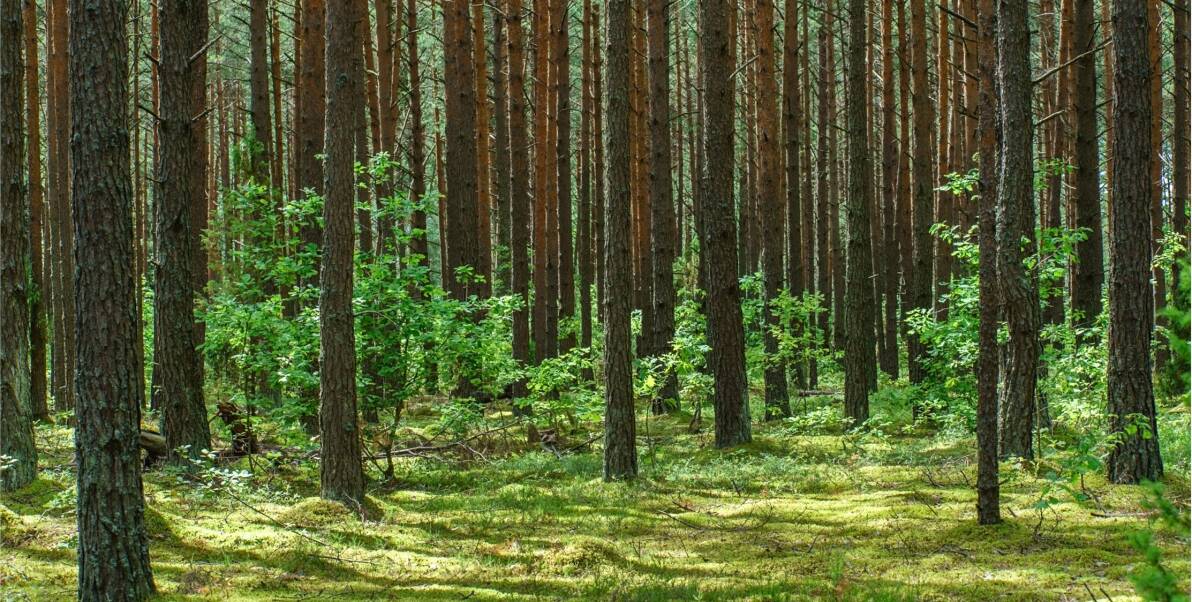
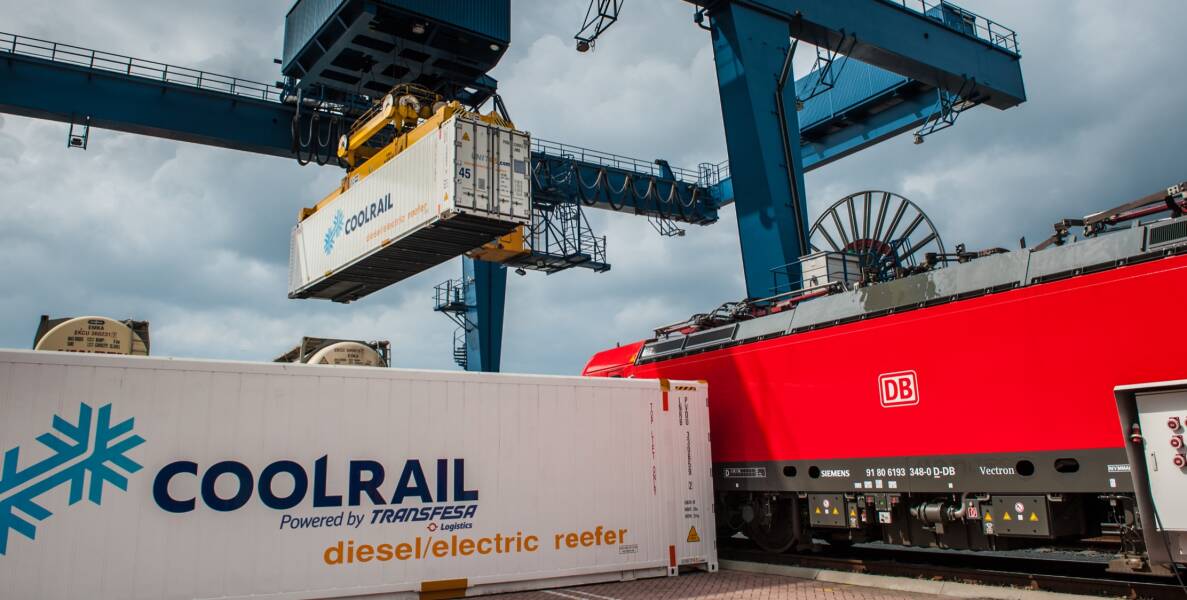
Reducing our carbon footprint
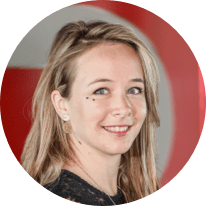
Céline Courrege
”When we are able to anticipate on the future needs of customers, we are able to optimise and improve sustainability”.
Through tooling we can optimise the flows of our pallets across Europe and anticipate any future needs of our customers. This helps us to optimise the transport process. “Having the right pallet at the right place at the right time is extremely relevant for all partners in the supply chain,” Céline explains. “We carefully determine the most optimal flow in terms of transport distance, costs and volumes.”
In addition to optimising the logistic flow, we also use tooling to select the best carriers, based on transport type and transport cost. As this requires less data entry, we gain a great deal of time that we can invest in analysis. Since last summer, LPR has also been using a transport price market tool to gain insight into transport prices and market trends. This is especially helpful to collect management information for new routes.
Tooling is also used to select more sustainable transport modalities. One of the tools gives access to a large database of carriers and actors, including multimodal transport. Sustainability criteria are also used in the selection of carriers. “For example, we can include criteria for trucks with a lower negative environmental impact,” Thibaut says. “The tools allow us to engage with suppliers we did not know before. We need suppliers who can propose alternative ways of working, such as using electric vehicles, so that we can find the right balance between sustainability and profitability.” An example is the short-sea shipping flow between the UK and Spain, and a new route using rail transport between the UK and Italy.
The tools help us to manage change, such as the impact of COVID-19, which has caused soaring customer demand. Besides COVID-19, there has also been the challenge posed by Brexit, especially for LPR. As the UK is no longer an EU country, all pallets entering and leaving the UK now require heat treatment in line with ISPM15 requirements. This has led to various logistic changes in our supply chain. To ensure a smoothly functioning supply chain, we need to include these changes in our optimisation runs. Céline adds, ”By anticipating the future needs of our customers, we can optimise the supply chain and improve its sustainability.” Tooling assists in managing complex situations, in being flexible and in identifying sustainable alternatives. This allows us – together with our partners – to continuously improve sustainability in the supply chain.
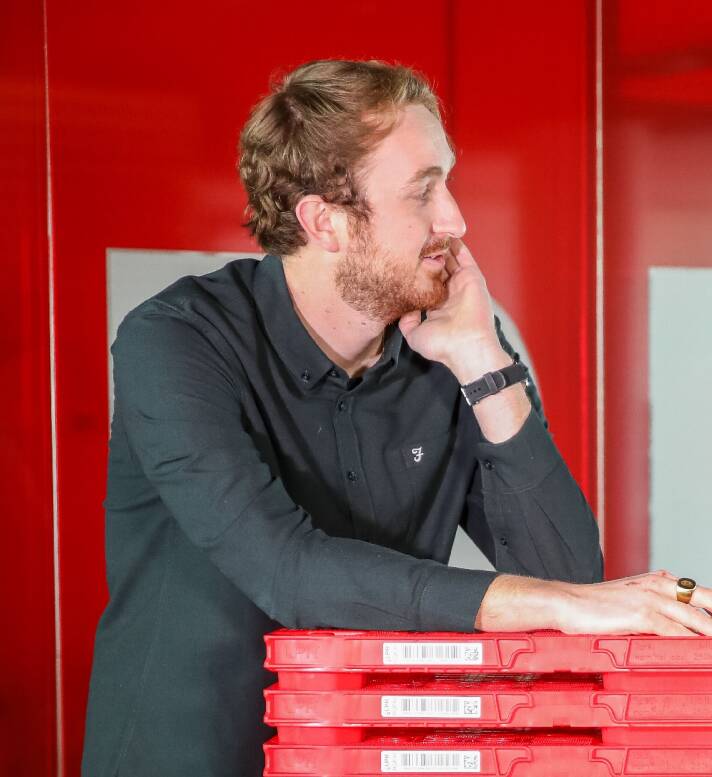
LPR uses innovative tools to optimise transport flows and use more sustainable transport modalities. Transport optimisation allows LPR to take on the role of sustainable catalyst in the supply chain. Two young professionals, Céline Courrege and Thibaut Bernabe, discuss the transport tools they use, and how they support sustainability in the supply chain.
Joint interview with Céline Courrege, Data Analyst Supply Chain at LPR and Thibaut Bernabe, Transport Analyst at LPR
Future-proof transport flows
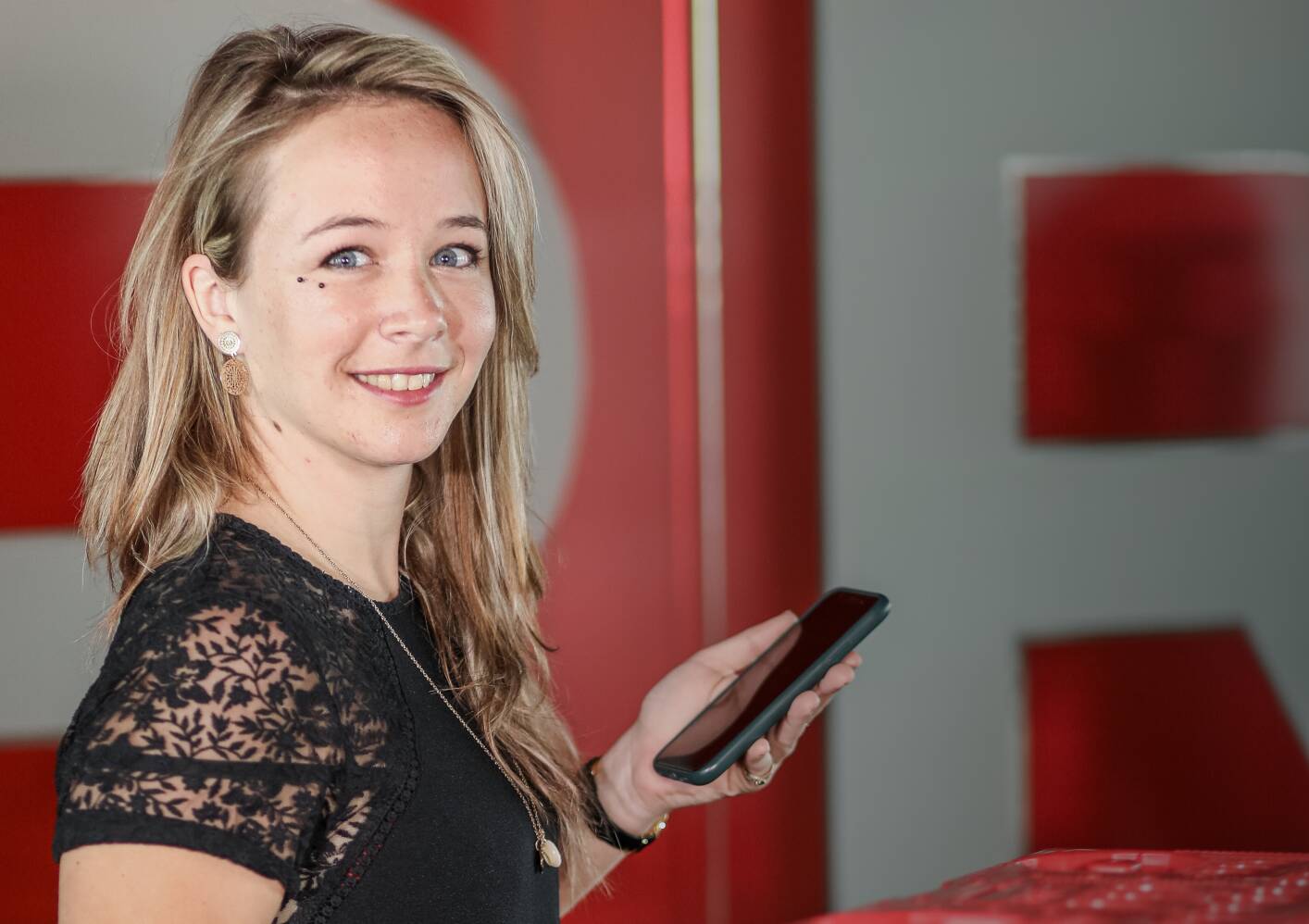

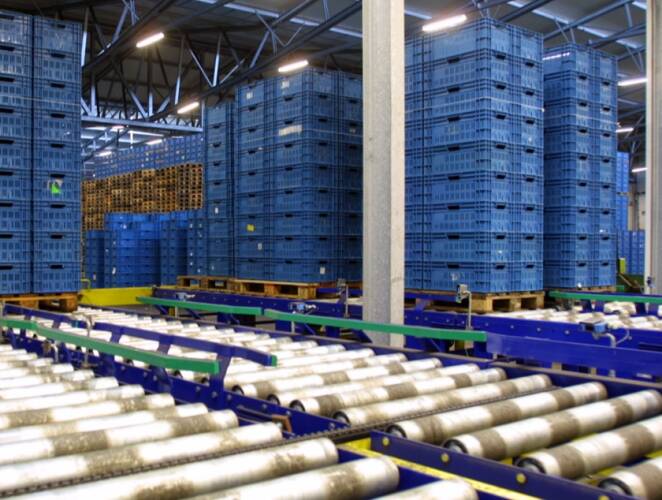
Hans De Bondt
“Switching to green folding trays has an enormous impact on the efficiency of EPS and our partners”
Rigid blue trays are still being used in the Benelux countries. A rigid blue tray occupies seven times more space than a folded green tray. This leads to inefficiencies in the supply chain, which is why the blue trays are being replaced by green folding trays. “As this transition drastically reduces transport movements and need for storage space, it will have an enormous impact on the efficiency of EPS and our partners,” Hans de Bondt explains. Smaller packaging allows for more trays to be transported with one truck. This means that there are fewer trucks on the road and more opportunities to combine transports, thus further reducing our carbon footprint.
Another benefit of the green trays is their full traceability in the supply chain. The trays are equipped with a barcode that is used to track their location. “This allows our customers to return their trays unsorted,” Hans tell us, “and this makes the return process much more efficient for them. The trays rotate faster, and less stock is needed while transport kilometres and costs are being reduced.” To enable the efficient rotation of unsorted returned trays, EPS upgraded the washing and receiving process at its depots. The new installations sort and wash the trays at high speed. The production of the new folding trays was started as early as 2018 in order to ensure enough stock to support the full transition. The old blue trays are now being collected and grinded. The granulate is 100% re-usable, and will be recycled partly for manufacturing new trays and partly as construction material for other purposes.
The first phase of transition started in February 2021. Since then, millions of blue trays have already been replaced. The second phase of the transition is scheduled for September 2021, when the auctions will also switch to green folding trays. EPS expects to recycle about 50 million blue trays in total. Many partners are involved in the project, including retailers, auction houses, logistic service providers and tray suppliers. “The large number of partners involved in the transition was challenging, but we worked together intensively to make the transition happen,” Hans says. “I am proud of the entire EPS team and delighted to see the immediate impact of the project on the sustainability of our supply chain!”
Project Cyan is the transition from rigid blue trays towards a new generation of green folding trays, which started in 2020. The project focuses on the Benelux countries and has an enormous impact on transport movements and CO2 reduction.
Interview with Hans De Bondt, Cyan Project Manager
Project Cyan:
a new generation of green trays
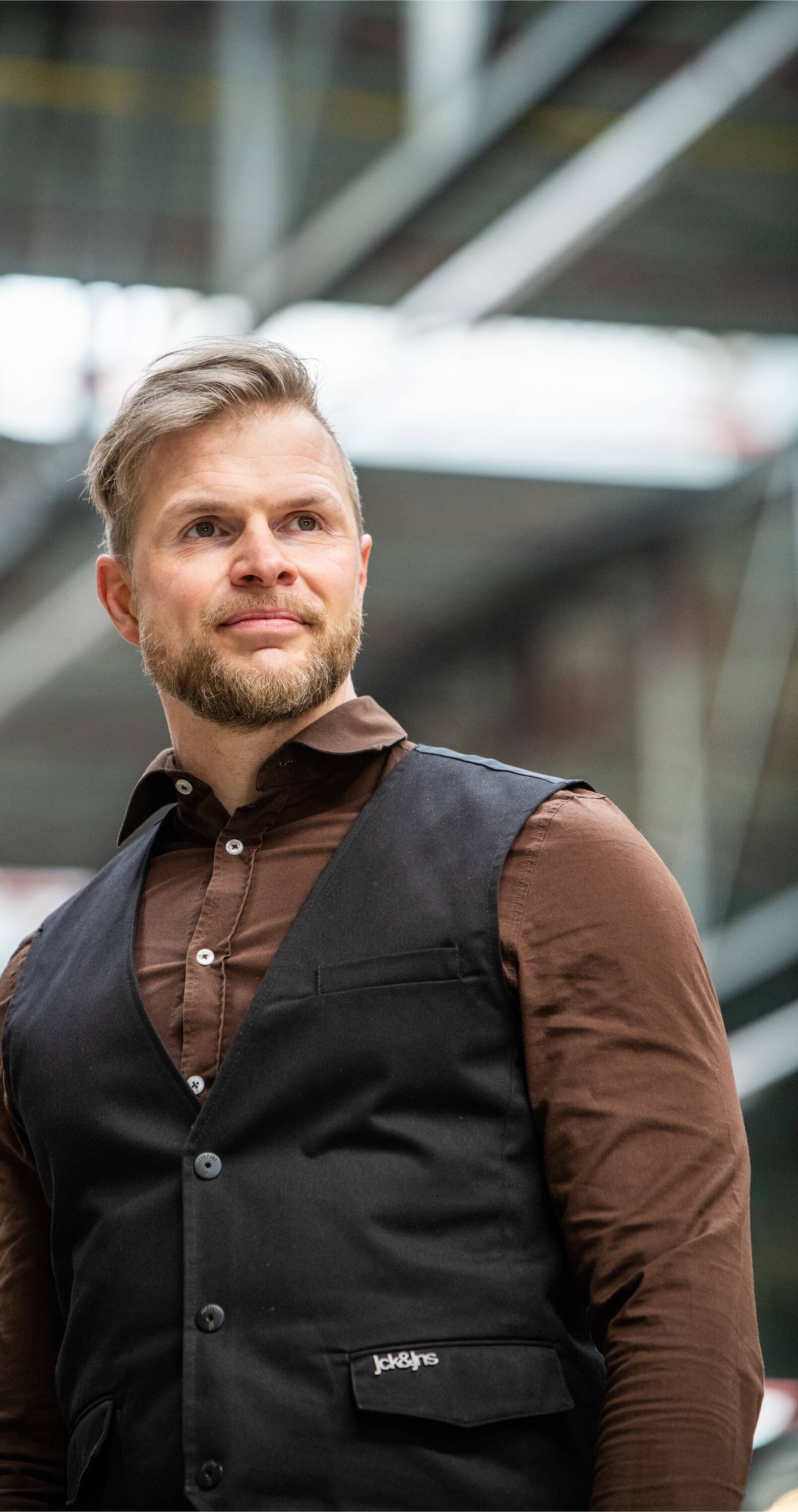
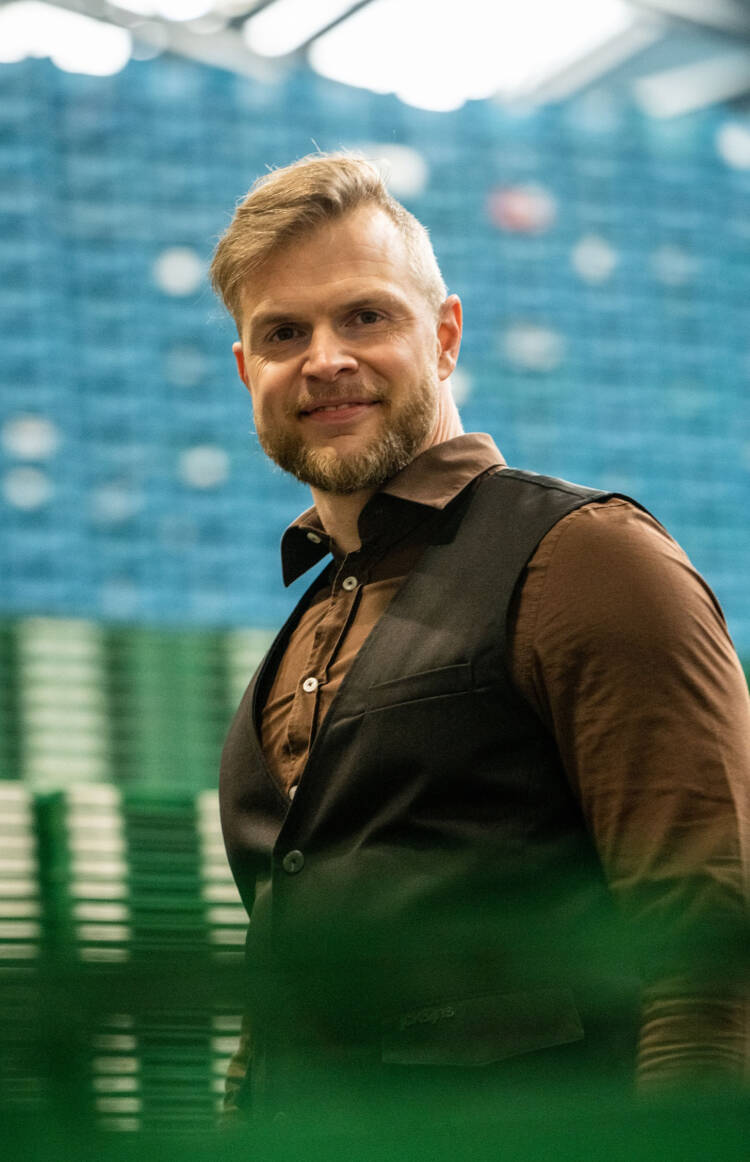
By increasing supply chain efficiency, deploying alternative modes of transport and designing our products optimally, we are reducing our carbon footprint and are contributing to the sustainability ambitions of our customers.
Planet


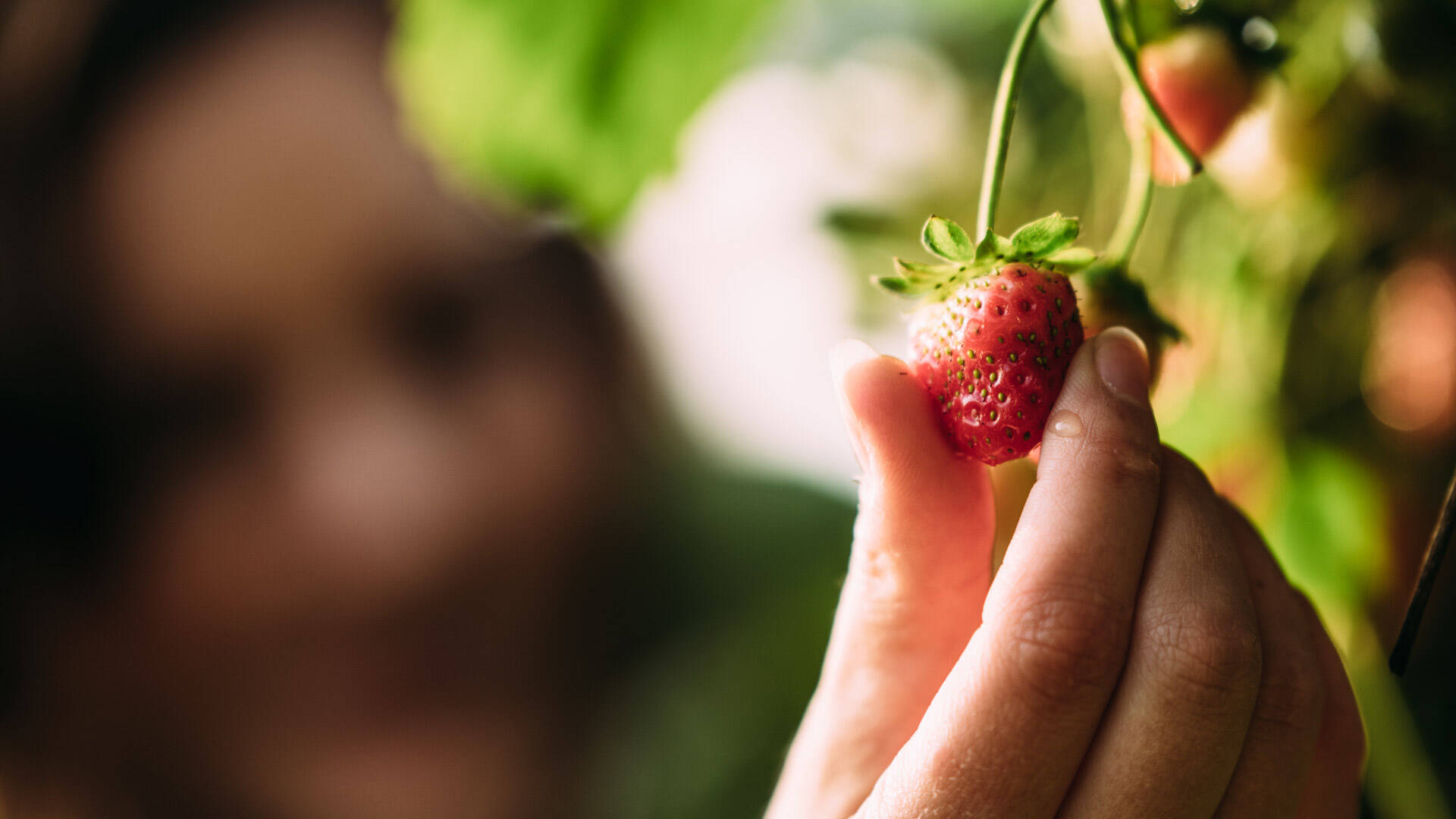