Summary of goals and results
Read more
Hyperloop Development Program
To stay ahead of innovations in logistics, EPS has joined the Hyperloop Development Program. This Dutch programme explores the realisation of a pan-European emission-free hyperloop network for cargo. Such a network would make it possible to transport goods over the ground at the speed of a plane. EPS joins as a knowledge partner and supports the development of this futuristic technology by contributing its experience to supply chain logistics.
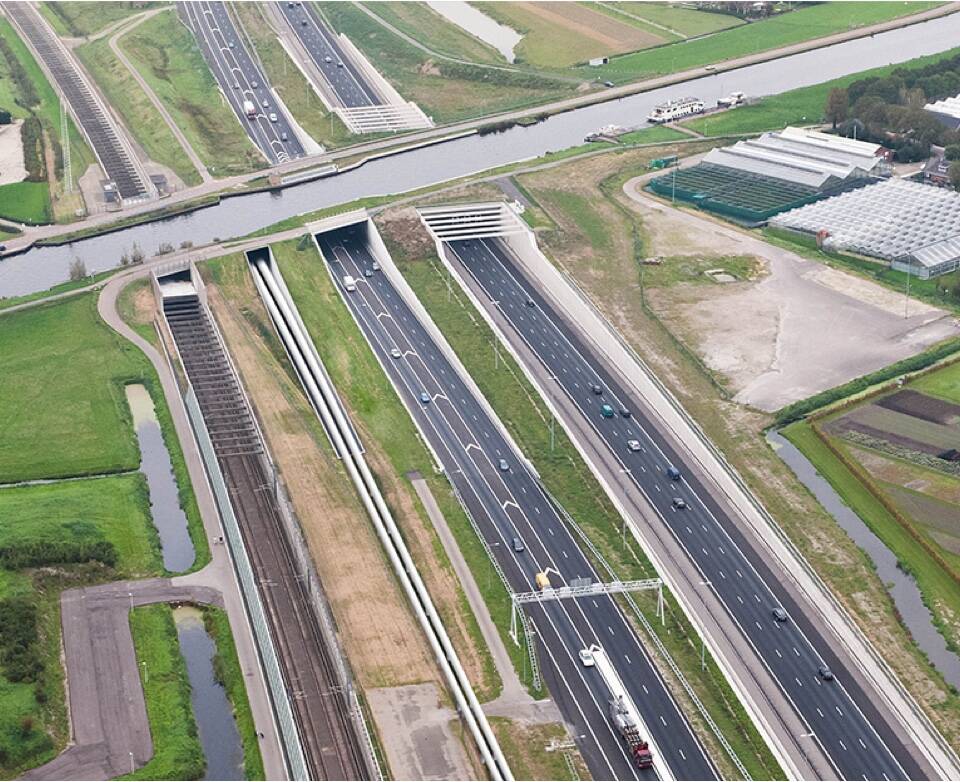
Euro Pool System
Supply chain analytics to track our carriers leads to smoother supplies. We are working together with our customers and knowledge partners in various pilots and initiatives to further optimise the supply chain of our customers. Last year, we continued developing smart tracking schemes in order to increase the traceability of our trays. Besides tracking individual trays using IoT, we also scan the trays at different locations. This gives us more insight into the movements throughout the supply chain. These insights are not only valuable to us, but even more so to our customers as these insights give them greater control over their stock of trays. In addition to tracking and optimising the flow of our carriers, we are also developing technology and services to monitor the quality of the fresh fruits and vegetables that we transport. This contributes to optimising the conditions within the supply chain and thus to reducing food waste.
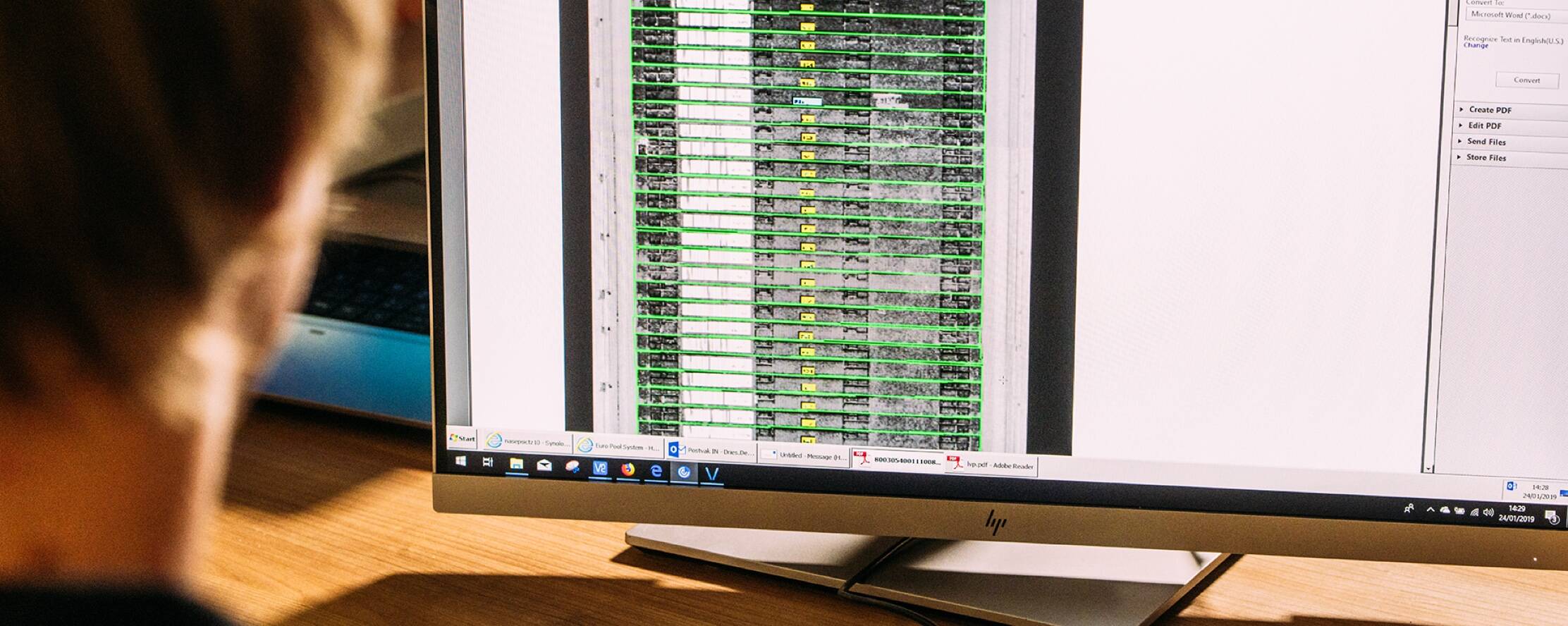
Read more
Stakeholders collaboration and dialogue in 2020
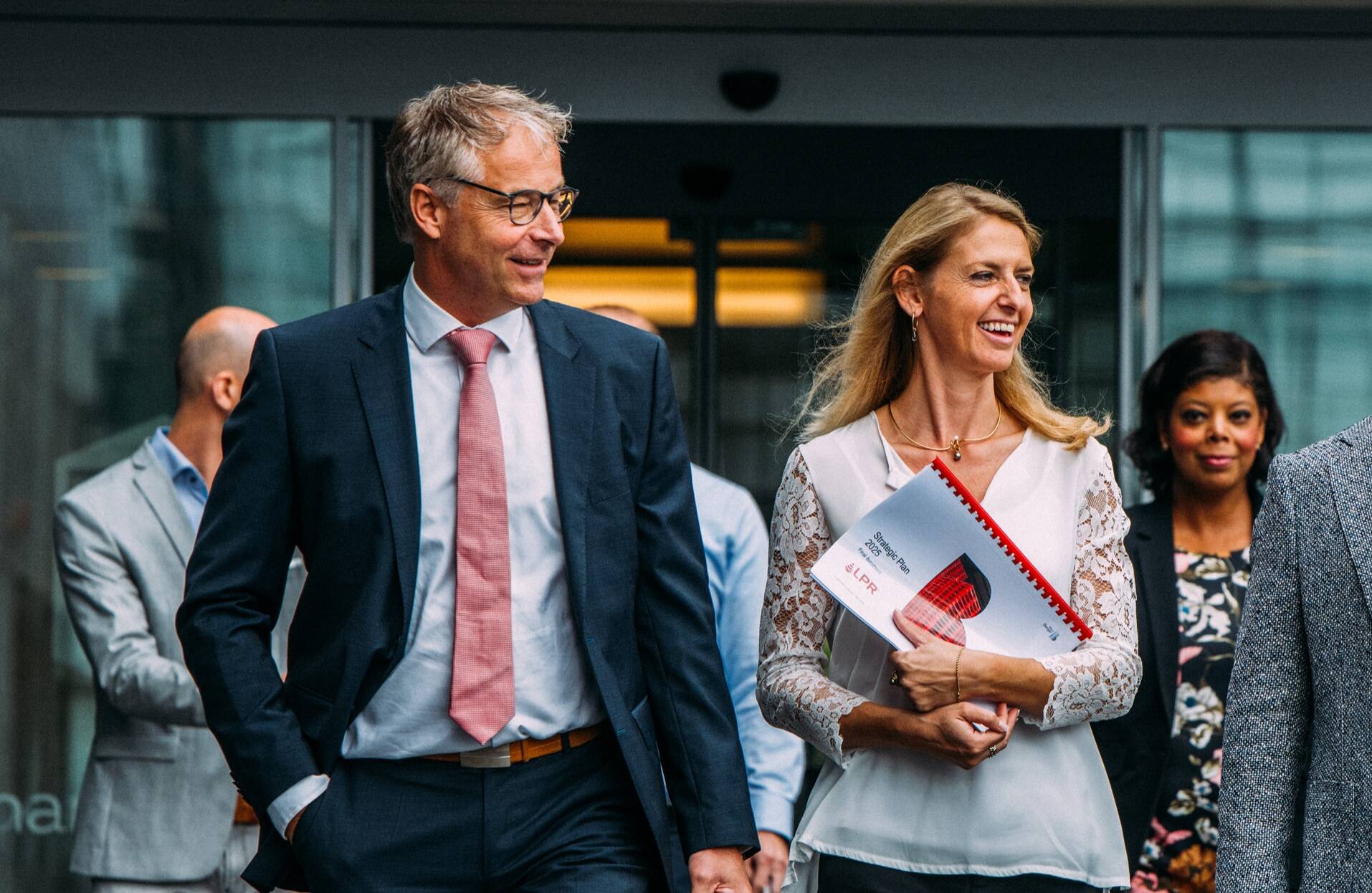
LPR is working on IoT applications and other traceability technologies to optimise the flow of pallets. In 2020, LPR continued with several pilots across Europe to monitor the movements of pallets in the supply chain and build knowledge about the benefits of traceability. We are working together with software developers, suppliers of tracking devices, customers, retail partners and the LPR depots. For these pilots we selected cases in which a relatively high number of pallets had been lost. Enhanced traceability provides insight and supports us, our customers and retailers in realising an efficient flow of pallets through the supply chain as well as in minimising losses. This will result in fewer pallets that need to be re-produced, and less uncontrolled pallet waste.
La Palette Rouge
Last year, LPR developed a new version of its plastic quarter pallet. The new model weighs 12% less than its predecessor. The lower weight means the pallet is easier and safer to handle, and less fuel is required for transport. The pallet was introduced in Poland in early 2020 and can now be found across Europe.
New plastic quarter pallet
To monitor the quality of our pallets more efficiently, LPR has developed the ‘Pallet Inspector’ device. This produces an automated 360 degree scan of the pallet and detects any defects in single pallets or a batch of pallets, allowing us to provide better quality pallets and better service to our customers. The Pallet Inspector also gives information on the exact dimensions of the pallet, which enables efficient stacking. The development of the Pallet Inspector is expected to be finalised in 2021.
Pallet inspector
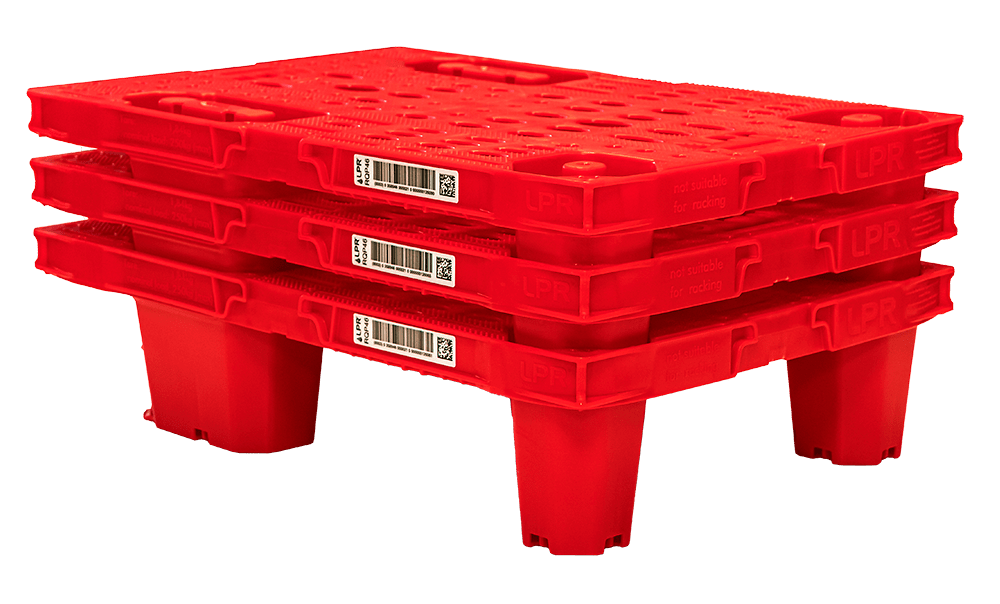

back to top
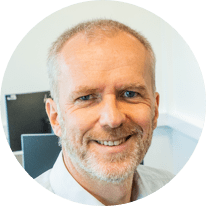
“We are located at the customer site, only 25 cm away to wash the trays”.
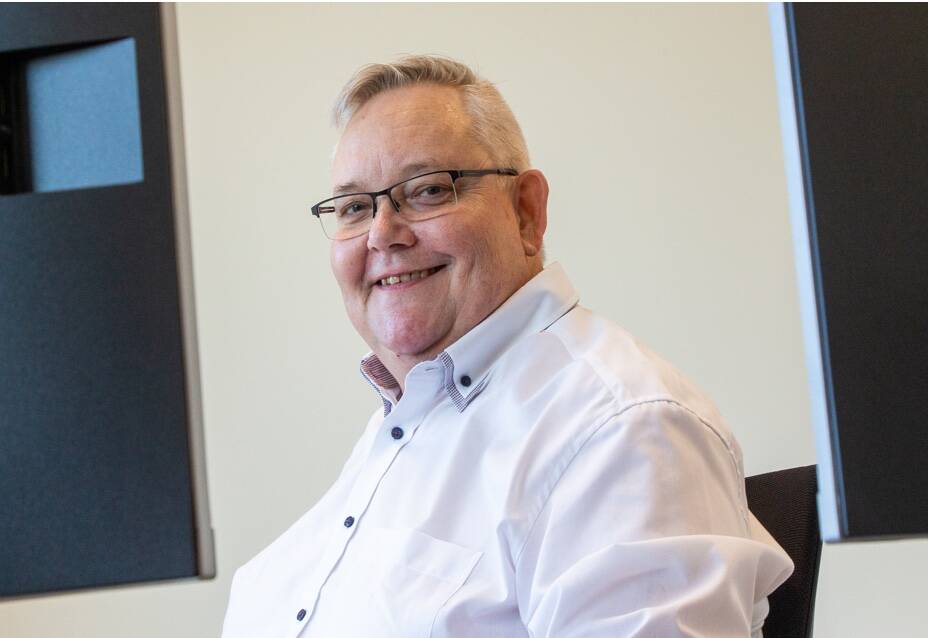
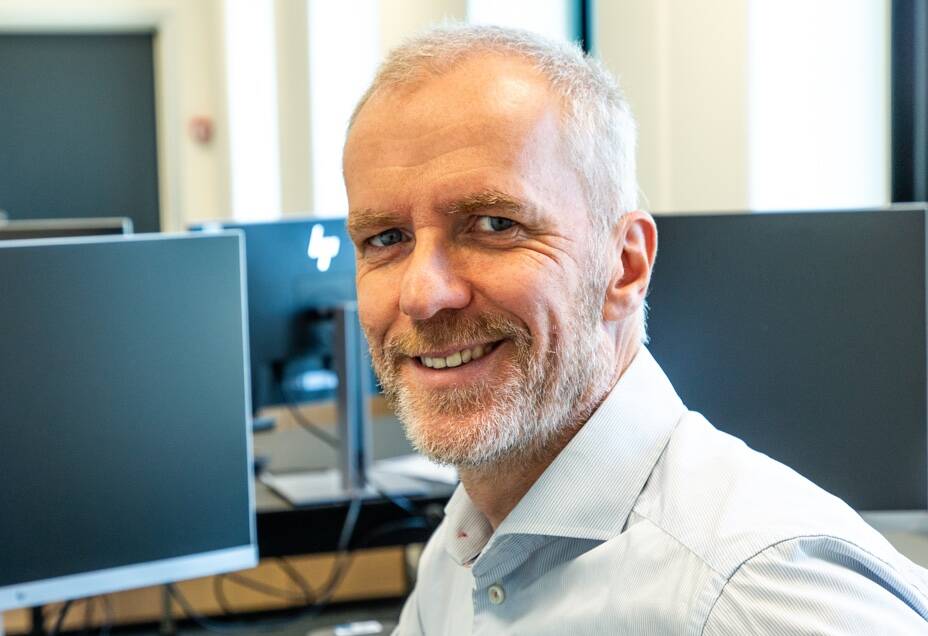
REMA 1000’s logistic site is located close to the city. “We want to add to the local community,” Ole explains. “We are keen to reduce noise and ensure environmental diversity on our site through attractive landscaping. Part of the site will also be open to joggers and to local schools to experience nature. The centre is also unique because it’s a real partnership between our companies. In the future there will be more positive spin-offs in running the site.” Michael agrees, “The partnership is key!”
The green reusable trays improve the sustainability performance of REMA 1000. However, after use the trays have to be returned to EPS’s washing facilities all around Europe. This is why REMA 1000 partnered with EPS to build a highly automated washing facility in the city of Horsens, Denmark. Located close to REMA’s shops and logistic centre, the new washing facility allows for a significant reduction in road transport. The facility was opened in November 2020. “We are located in the same building as REMA, and there is only a 25 cm thick wall between our washing process and REMA,” Michael Buskbjerg explains. “Every time a truck comes to the return centre, it can be serviced in one go. This is the most efficient way to work with our trays.” Ole Thomson agrees. “Our role is to provide a building that allows environmentally-friendly and efficient handling. We are running a business in a competitive environment. This joint venture strengthens our business by lowering costs, and it has a positive impact on the environment.” Michael adds, “At EPS we are efficient at running our operation while caring for the environment at the same time. We clean the water to make sure that we are washing the trays in an efficient and environmentally-friendly way, and we clean the water again once it leaves our operation. There are solar panels on the roof that power both our operations.”
The green reusable trays improve the sustainability performance of REMA 1000. However, the used trays had to be returned to Euro Pool System washing facilities all around Europe. That’s why REMA 1000 partnered with Euro Pool System to build a highly automated washing facility in the city of Horsens, Denmark. Close to its shops and logistical centre, thereby significantly reducing unnecessary road transport. It was opened in November 2020.
REMA 1000 is a retailer with 350+ stores in Denmark, and has been a partner of Euro Pool Systems for many years. REMA 1000 uses 40,000 trays every day to transport fresh fruit and vegetables to their discount stores.
Joint interview with Ole Thomsen, Director of Logistics at REMA 1000, and Michael Buskbjerg, Regional Commercial Manager at EPS Nordics
Building a a tray washing facility with REMA 1000
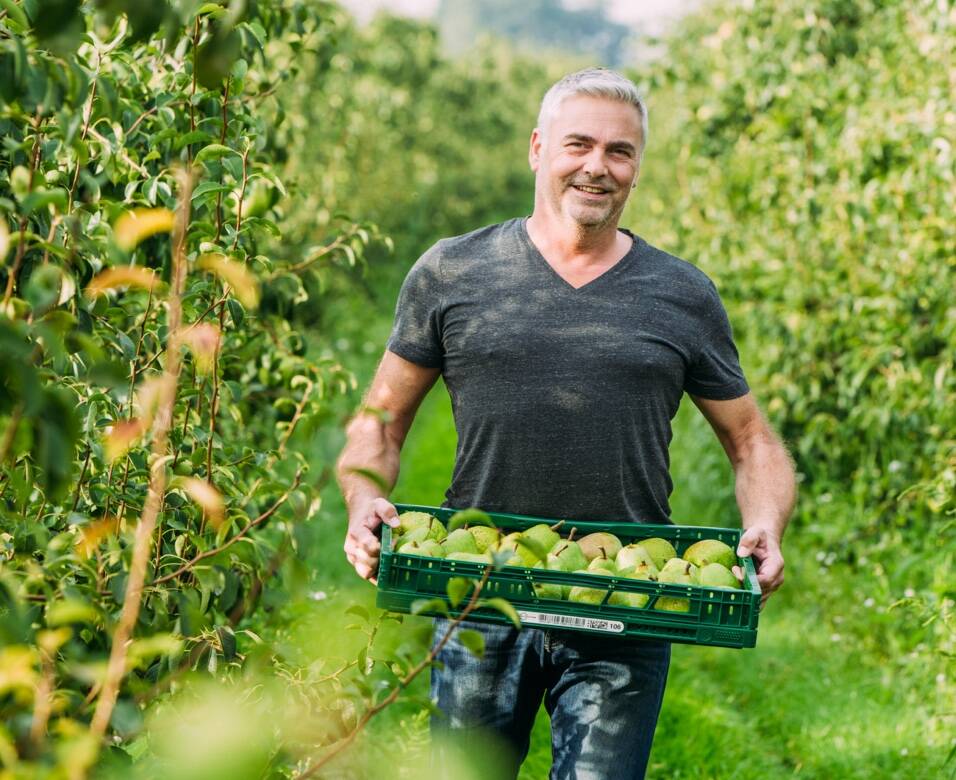
We are working closely with our customers and partners to create shared value and to work towards a positive impact throughout the supply chain by sharing the benefits of reusable packaging solutions.
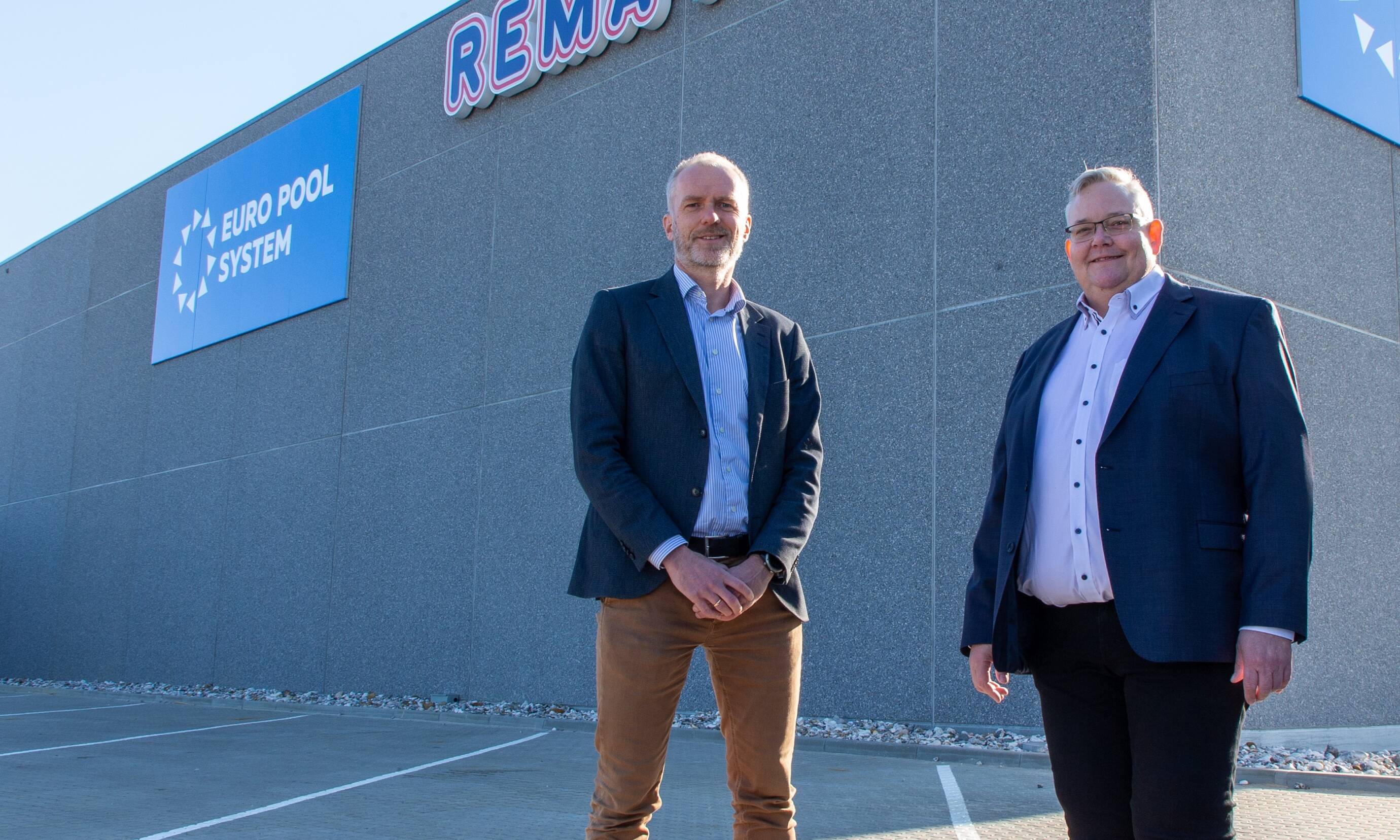
Read more
Partners

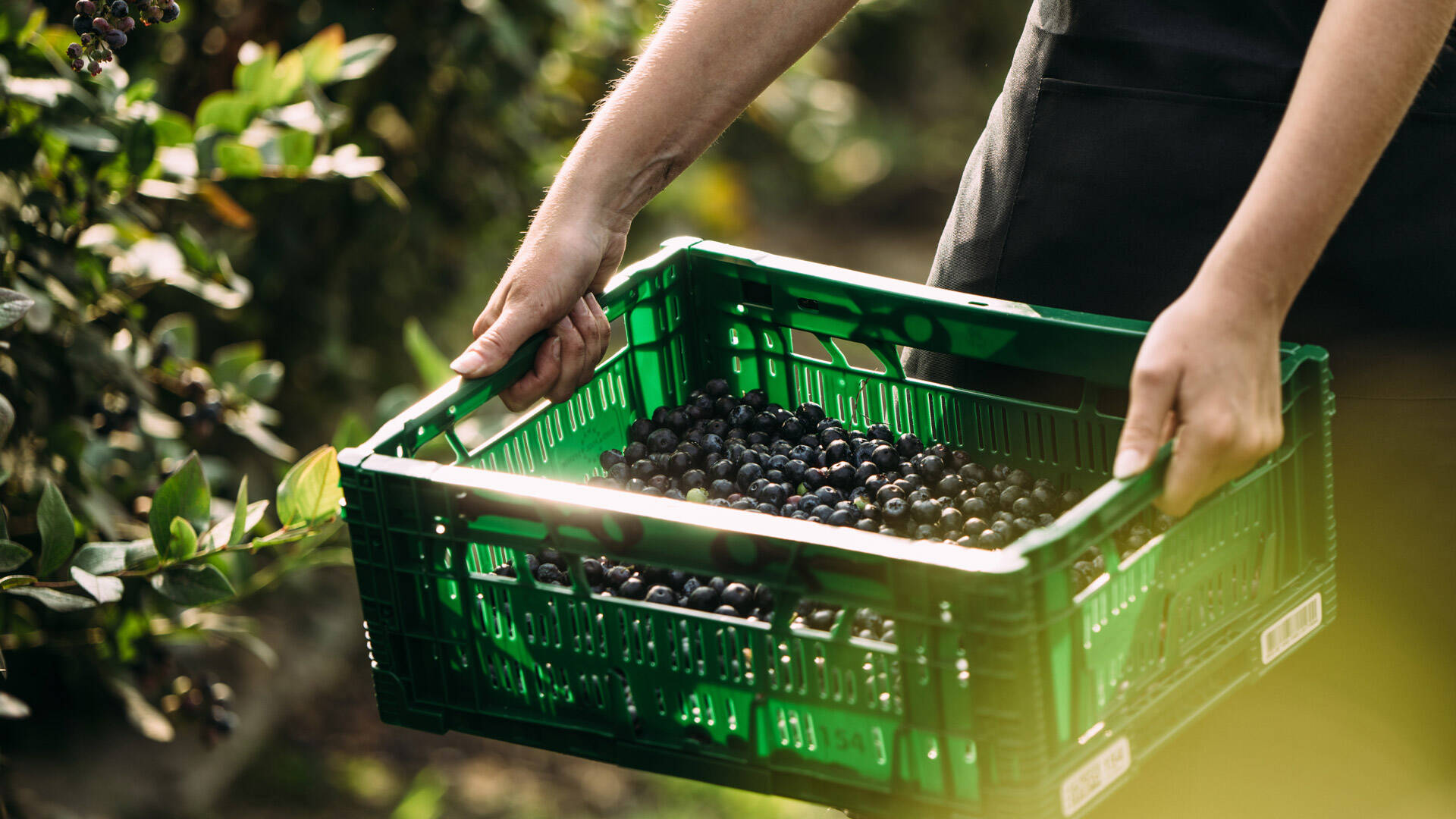
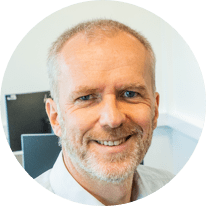
“We are located at the customer site, only 25 cm away to wash the trays”.
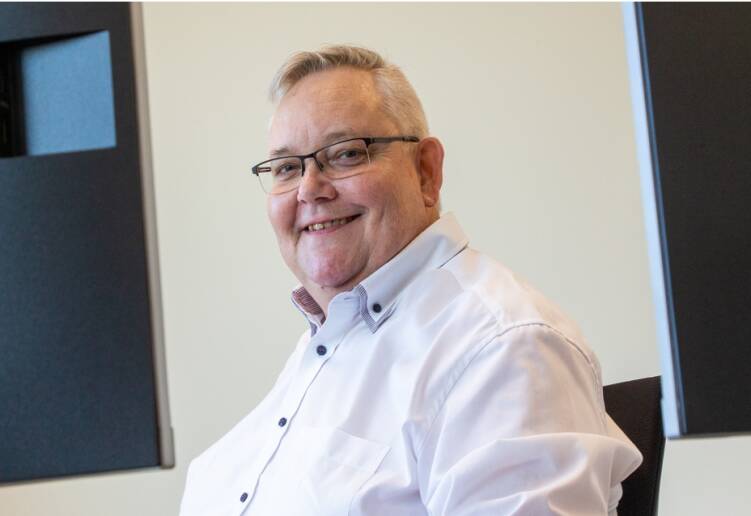
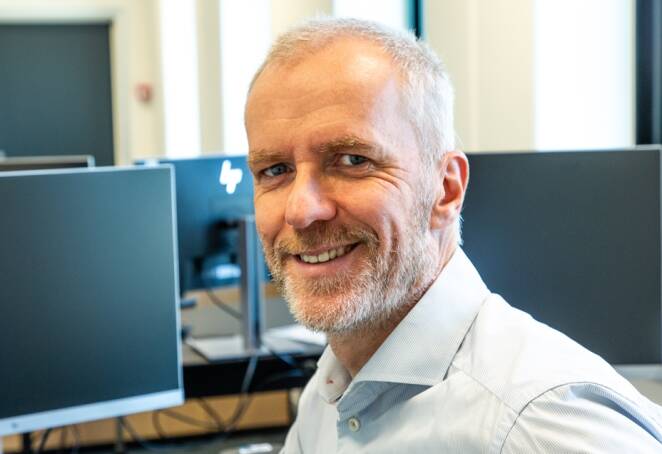
REMA 1000’s logistic site is located close to the city. “We want to add to the local community,” Ole explains. “We are keen to reduce noise and ensure environmental diversity on our site through attractive landscaping. Part of the site will also be open to joggers and to local schools to experience nature. The centre is also unique because it’s a real partnership between our companies. In the future there will be more positive spin-offs in running the site.” Michael agrees, “The partnership is key!”
The green reusable trays improve the sustainability performance of REMA 1000. However, after use the trays have to be returned to EPS’s washing facilities all around Europe. This is why REMA 1000 partnered with EPS to build a highly automated washing facility in the city of Horsens, Denmark. Located close to REMA’s shops and logistic centre, the new washing facility allows for a significant reduction in road transport. The facility was opened in November 2020. “We are located in the same building as REMA, and there is only a 25 cm thick wall between our washing process and REMA,” Michael Buskbjerg explains. “Every time a truck comes to the return centre, it can be serviced in one go. This is the most efficient way to work with our trays.” Ole Thomson agrees. “Our role is to provide a building that allows environmentally-friendly and efficient handling. We are running a business in a competitive environment. This joint venture strengthens our business by lowering costs, and it has a positive impact on the environment.” Michael adds, “At EPS we are efficient at running our operation while caring for the environment at the same time. We clean the water to make sure that we are washing the trays in an efficient and environmentally-friendly way, and we clean the water again once it leaves our operation. There are solar panels on the roof that power both our operations.”
The green reusable trays improve the sustainability performance of REMA 1000. However, the used trays had to be returned to Euro Pool System washing facilities all around Europe. That’s why REMA 1000 partnered with Euro Pool System to build a highly automated washing facility in the city of Horsens, Denmark. Close to its shops and logistical centre, thereby significantly reducing unnecessary road transport. It was opened in November 2020.
REMA 1000 is a retailer with 350+ stores in Denmark, and has been a partner of Euro Pool Systems for many years. REMA 1000 uses 40,000 trays every day to transport fresh fruit and vegetables to their discount stores.
back to top
Summary of goals and results
Read more
Stakeholders collaboration and dialogue in 2020
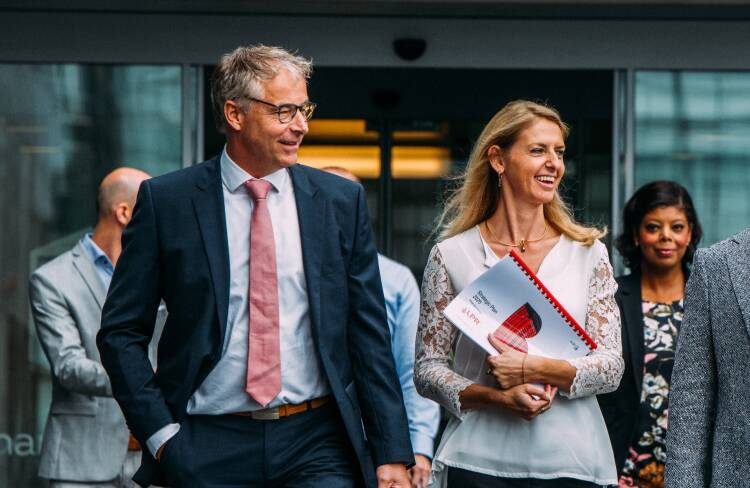
Hyperloop Development Program
To stay ahead of innovations in logistics, EPS has joined the Hyperloop Development Program. This Dutch programme explores the realisation of a pan-European emission-free hyperloop network for cargo. Such a network would make it possible to transport goods over the ground at the speed of a plane. EPS joins as a knowledge partner and supports the development of this futuristic technology by contributing its experience to supply chain logistics.
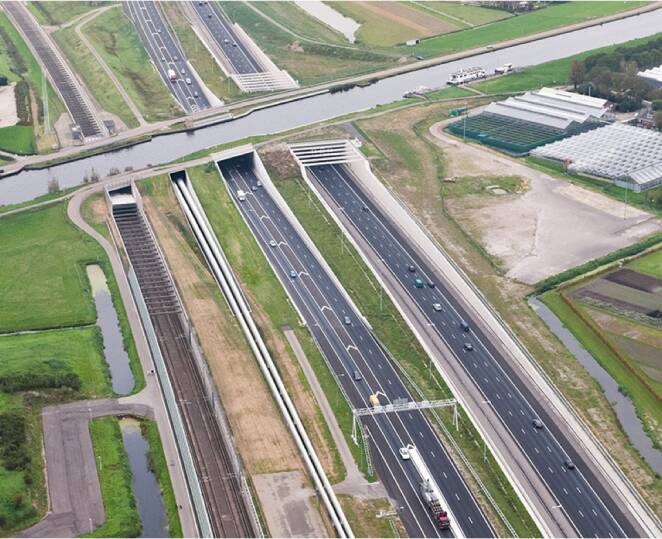
Euro Pool System
Supply chain analytics to track our carriers leads to smoother supplies. We are working together with our customers and knowledge partners in various pilots and initiatives to further optimise the supply chain of our customers. Last year, we continued developing smart tracking schemes in order to increase the traceability of our trays. Besides tracking individual trays using IoT, we also scan the trays at different locations. This gives us more insight into the movements throughout the supply chain. These insights are not only valuable to us, but even more so to our customers as these insights give them greater control over their stock of trays. In addition to tracking and optimising the flow of our carriers, we are also developing technology and services to monitor the quality of the fresh fruits and vegetables that we transport. This contributes to optimising the conditions within the supply chain and thus to reducing food waste.
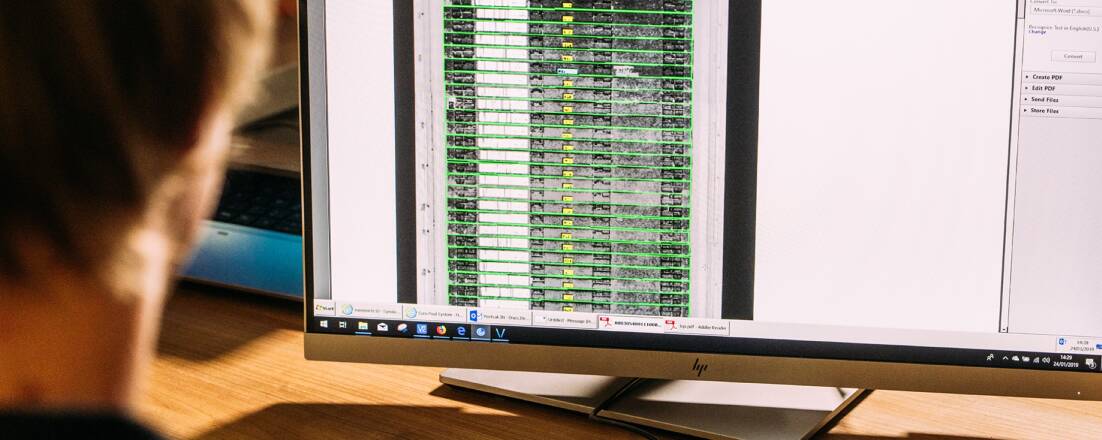
LPR is working on IoT applications and other traceability technologies to optimise the flow of pallets. In 2020, LPR continued with several pilots across Europe to monitor the movements of pallets in the supply chain and build knowledge about the benefits of traceability. We are working together with software developers, suppliers of tracking devices, customers, retail partners and the LPR depots. For these pilots we selected cases in which a relatively high number of pallets had been lost. Enhanced traceability provides insight and supports us, our customers and retailers in realising an efficient flow of pallets through the supply chain as well as in minimising losses. This will result in fewer pallets that need to be re-produced, and less uncontrolled pallet waste.
La Palette Rouge
Last year, LPR developed a new version of its plastic quarter pallet. The new model weighs 12% less than its predecessor. The lower weight means the pallet is easier and safer to handle, and less fuel is required for transport. The pallet was introduced in Poland in early 2020 and can now be found across Europe.
New plastic quarter pallet
To monitor the quality of our pallets more efficiently, LPR has developed the ‘Pallet Inspector’ device. This produces an automated 360 degree scan of the pallet and detects any defects in single pallets or a batch of pallets, allowing us to provide better quality pallets and better service to our customers. The Pallet Inspector also gives information on the exact dimensions of the pallet, which enables efficient stacking. The development of the Pallet Inspector is expected to be finalised in 2021.
Pallet inspector
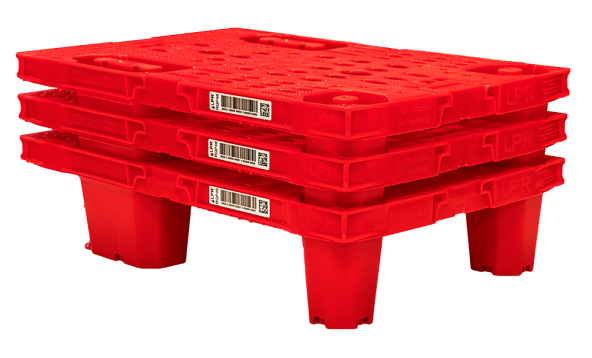
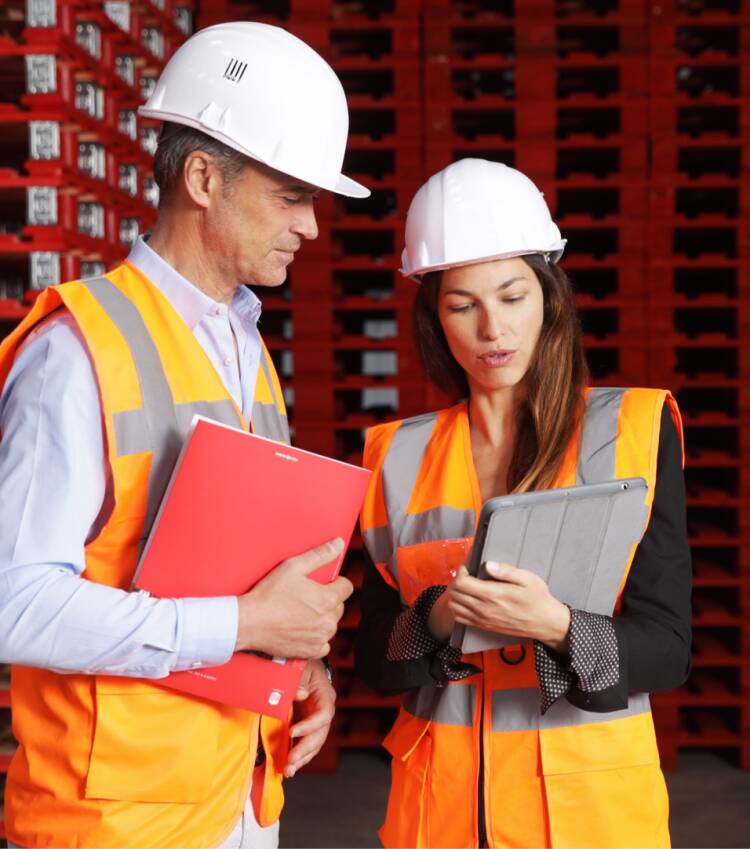
Joint interview with Ole Thomsen, Director of Logistics at REMA 1000, and Michael Buskbjerg, Regional Commercial Manager at EPS Nordics
Building a a tray washing facility with REMA 1000
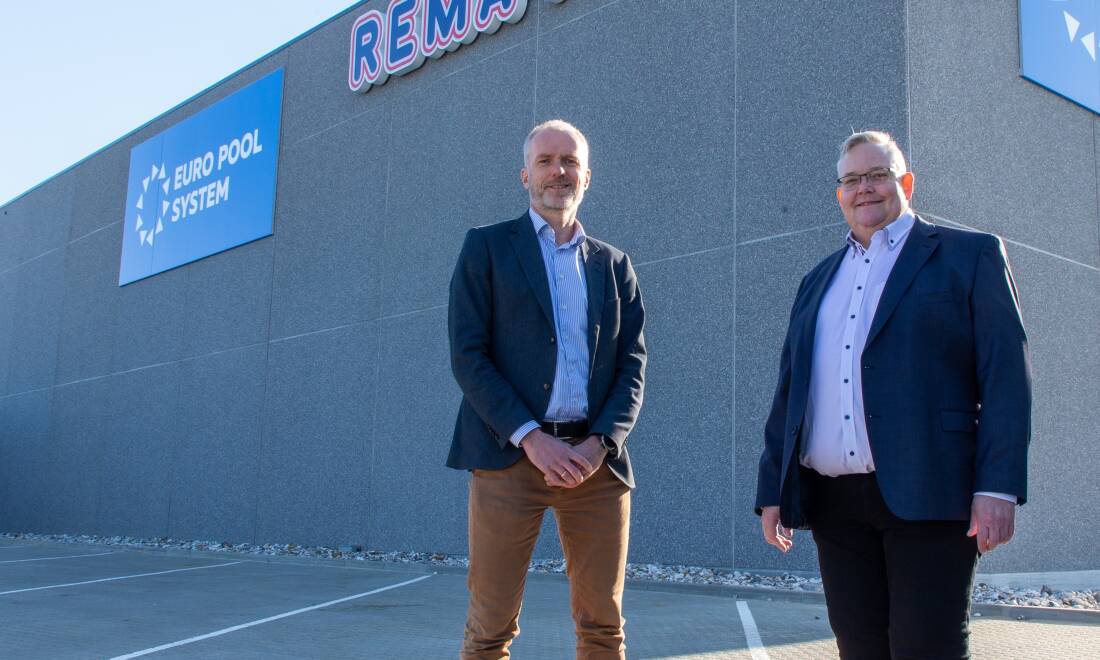
We are working closely with our customers and partners to create shared value and to work towards a positive impact throughout the supply chain by sharing the benefits of reusable packaging solutions.
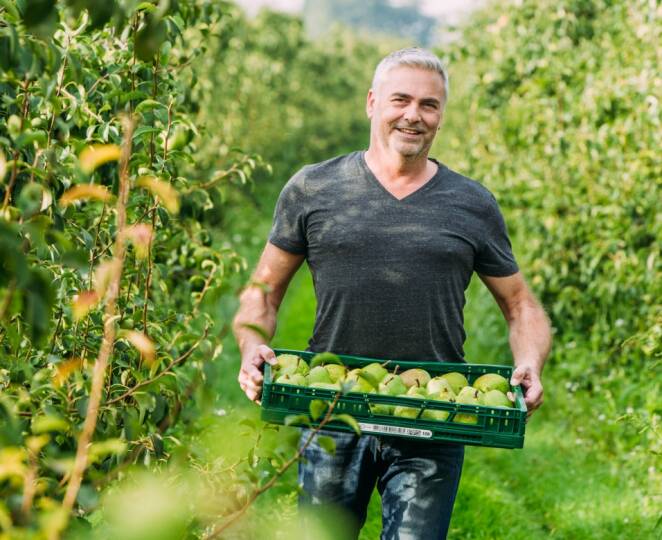
Partners

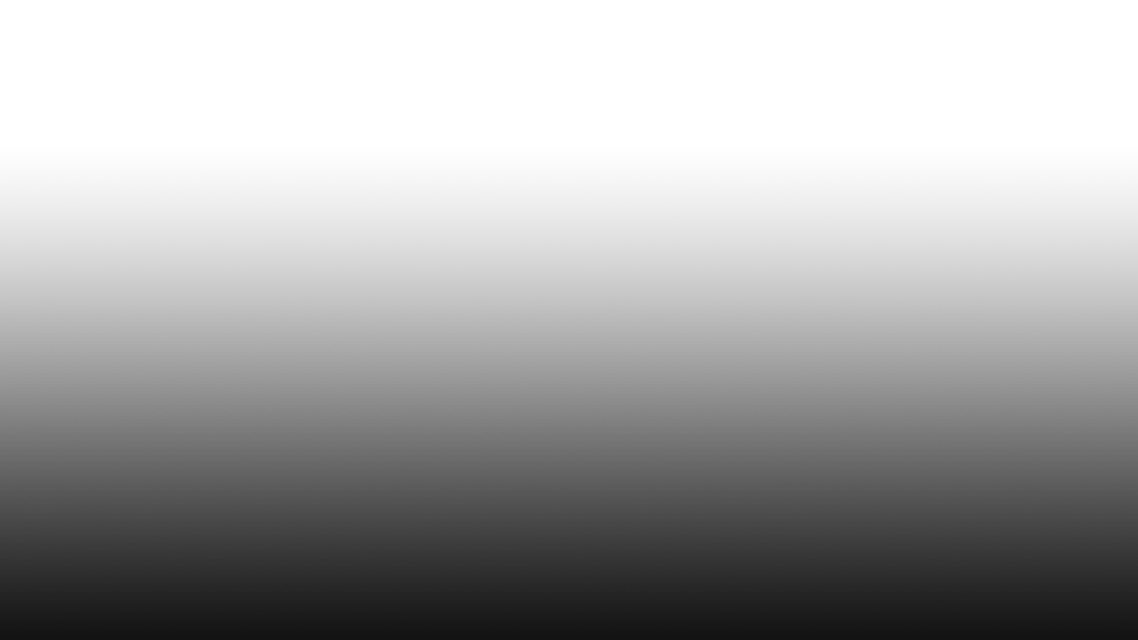
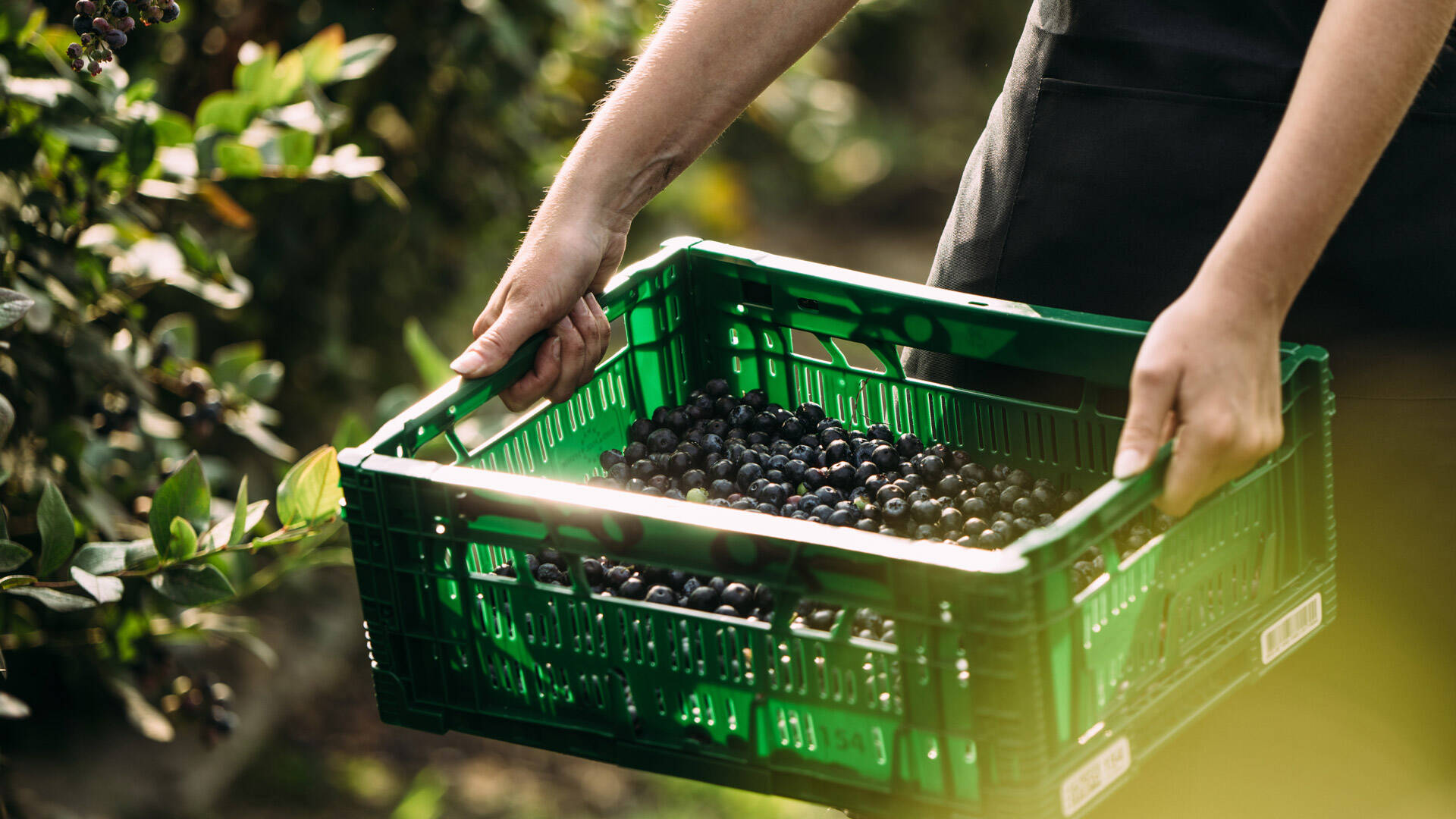